The BIM4 H&S Working Group has developed new guidance for those procuring projects which should enable the project and design teams to identify significant issues and risks early. One of its authors, strategic technical adviser Steve Coppin, explains more.
New guidance from the BIM4 Health and Safety Working Group will help clients discharge their duties under the CDM Regulations more easily by harnessing the standard building information management protocols. The working group is chaired by Gordon Crick, an inspector at the Health & Safety Executive (HSE).
Its title is CDM Digitally – Guidance to Help all Clients: Improving information management in construction projects and its purpose is to educate and inform clients on how relevant data information can be captured and shared with the right people at the right times during the life cycle of their projects.
The guidance sets out why and how clients should adopt information management (IM) and information requirements (IMRs) in the contract via employer’s information requirements (EIRs) as part of the procurement process and set this out in the brief at the earliest stage of the project.
Identifying risks early
Setting out information requirements enables the project and design teams to identify significant issues and risks early and enables building elements to be captured and tracked during the life cycle of any project. This helps assist in complying with the legal requirements of CDM.
Better information management methodologies provide effective ways of meeting these requirements – for example, clash detection can identify significant health and safety issues and risks in early design, opening up new possibilities for monitoring and measuring risk management, including better learning opportunities.
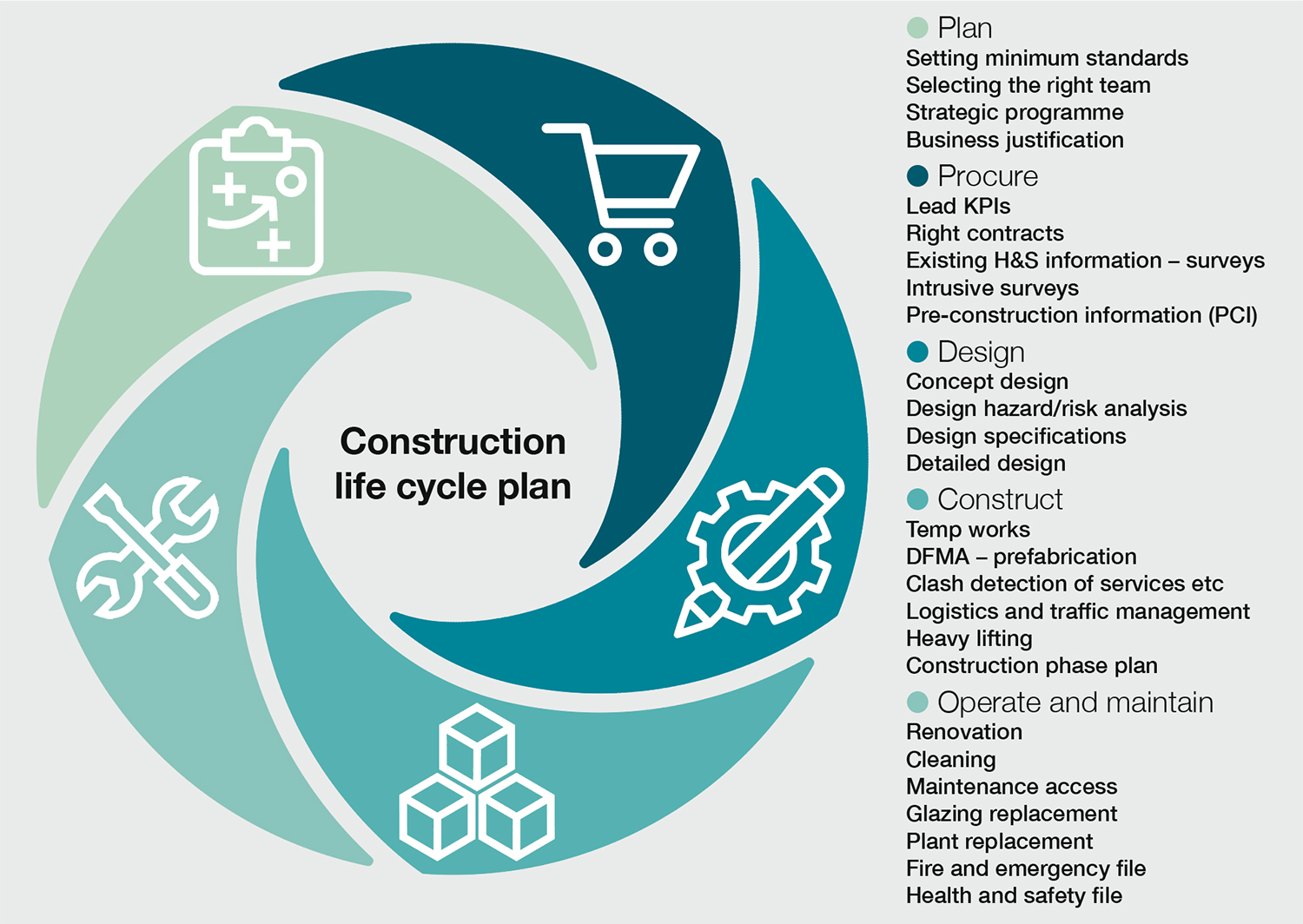
Four key benefits include:
- from 3D to 4D and, better still, geometric models of structures in the early design phases provide visual pictures and animations which enhance the foreseeability of significant risks. (Duties on designers in CDM Regs 9 & 11);
- 4D and, better still, geometric animations and simulations, which show construction over time, enable designs to be tested, rehearsed and checked, where stages of work take place successively and simultaneously (CDM Reg 11);
- development of an effective common data environment (CDE) enables co-ordination for the purpose of planning, managing monitoring and coordination of critical health and safety information on a project
- (CDM Regs 11 and 13); and
- handover of an effective health and safety file is enabled by good information management (CDM Reg 4).
Bridging PAS 1192-6 and ISO 19650
The PAS document PAS 1192-6 sets out the protocol for adopting a common data environment which allows information to be shared between the team and then handed over to the client in a standard format when the project is completed.
This helps clients improve information management for any construction project for their existing and future assets. The principles can be adopted for a paper-based system or improving the industry through better use of digital technology.
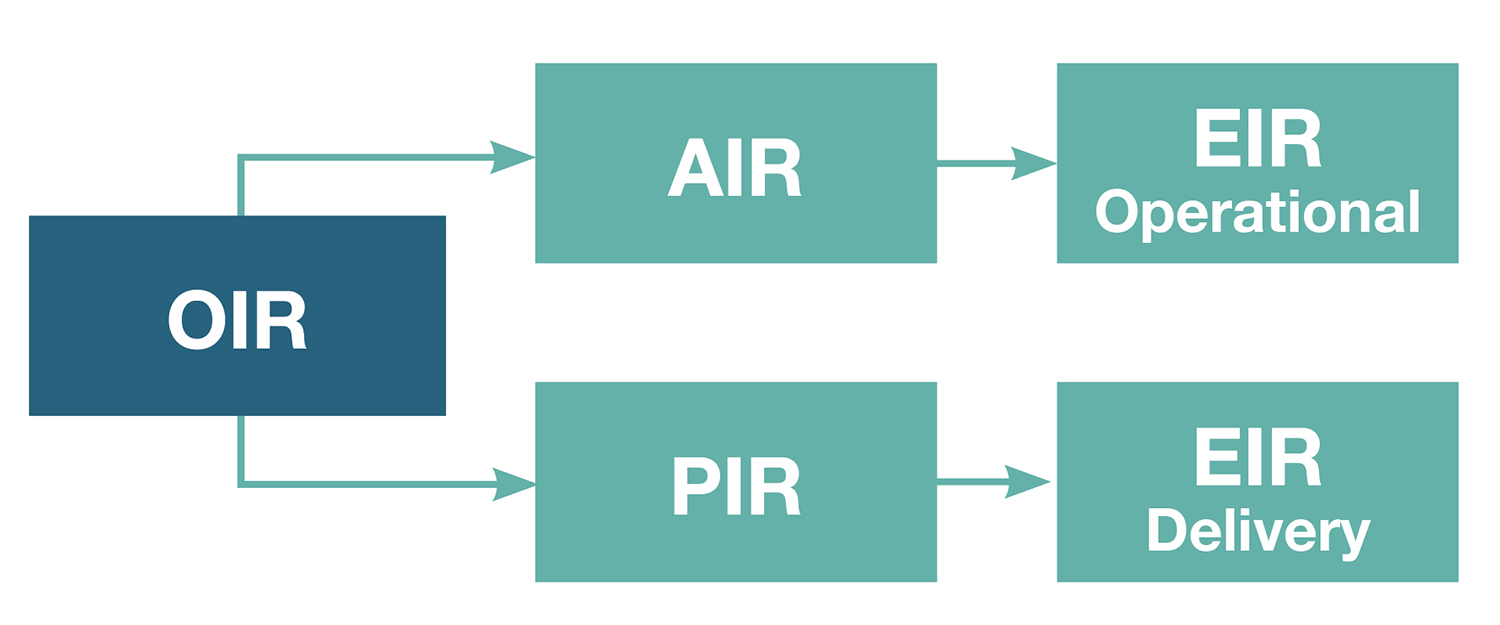
The protocol set out in PAS 1192-6 is then added to, with 10 plain language questions that will help clients identify and prioritise key health and safety issues and risks. That is, focusing on good risk management, from project inception to design and construction and on to operational use of the asset.
The questions have an associated maturity matrix to help clients fully understand them and prompt solutions and actions they might consider and or be required to perform.
Embedded BIM standard
The context for this guidance is that the new ISO 19650 standard is now embedded as the new BIM standard. It replaces the PAS documents, but, for health and safety, the PAS 1192-6: 2018 standard is the only part of the 1192 series which remains. Work is in hand to convert this to ISO 19650 Part 6, but this will not be completed before 2024.
The good news is that ISO 19650 proves to be a very useful vehicle for taking forward health and safety information management and can be used to fulfil the spirit and purpose of 1192 Part 6. Underlying this is a common spirit and purpose with the CDM 2015 regulations – to provide the right information to the right people at the right times of the project life cycle.
The ISO 19650 approach requires some new terminology. The client becomes the ‘appointing party’, while a principal designer or principal contractor, who must be appointed directly by the client, will be a ‘lead appointed party’.
New terminology
Perhaps most fundamentally, the EIR is now redefined as ‘exchange information requirements’. Although the acronym remains the same, the purpose is different, in that EIRs in ISO 19650 terms are detailed information requirements derived from higher level project information requirements (PIRs) and asset information requirements (AIRs).
At the head of the information requirements chain are organisational requirements, which set out at the highest level the information the client needs to run their business. In health and safety terms the organisational information requirements (OIRs) will probably equate to statements you might find in a board-level health and safety policy document.
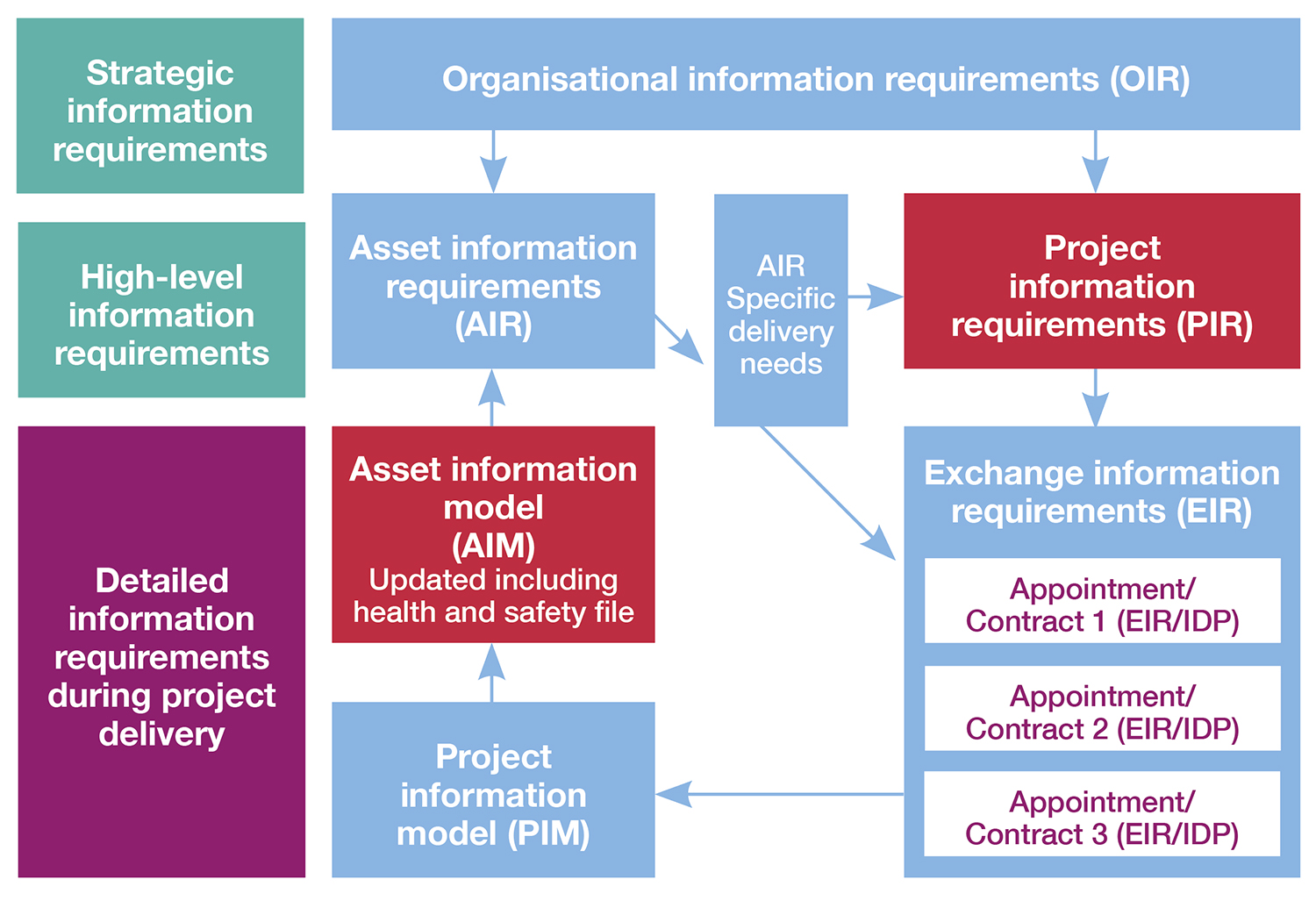
The clients’ guidance stresses the need for a line of sight from the high-level requirement down to the detailed point of delivery of information in a project. In this way a client is assured that the digital products specified will actually be delivered and that the client and other dutyholders, under the CDM15, are properly fulfilling their legal duties, rather than transferring them blindly to another party.
Triangle of expertise
The guidance shows how PIRs should reflect the legal duties of a client and that PIRs can be drafted to emphasise the fact that it should be the client (as head of procurement and funding the project) calling the shots.
Ideally, a triangle of expertise – representing the client, principal designer and information manager – should develop a suite of appropriate information requirements for a project, right at the outset.
Both the PIRs for the project delivery and the AIRs for any asset replacement should be in the client’s procurement strategy and specified in the contract by the appointing party (the appointing body is the client through the EIRs).
Annex B of the UK BIM Framework’s ISO 19650 Guidance Part D: Developing Information Requirements sets out five examples of how information requirements for health and safety may be developed. These give some detail on how an EIR should be developed.
The topics are:
- asbestos;
- being an exemplar organisation in managing elevated risk;
- recording details of safety critical suppliers;
- producing an effective health and safety file; and
- managing risks of high-level glazing.
What are the next steps?
We hope this will help clients and their project teams utilise digital resources to land and embed health and safety considerations within their projects for their assets and to start piloting the approach that has been set out and capture the learning.
A copy of the current draft guidance is available via [email protected].
Steve Coppin is strategic technical adviser of SJC Risk Management Solutions