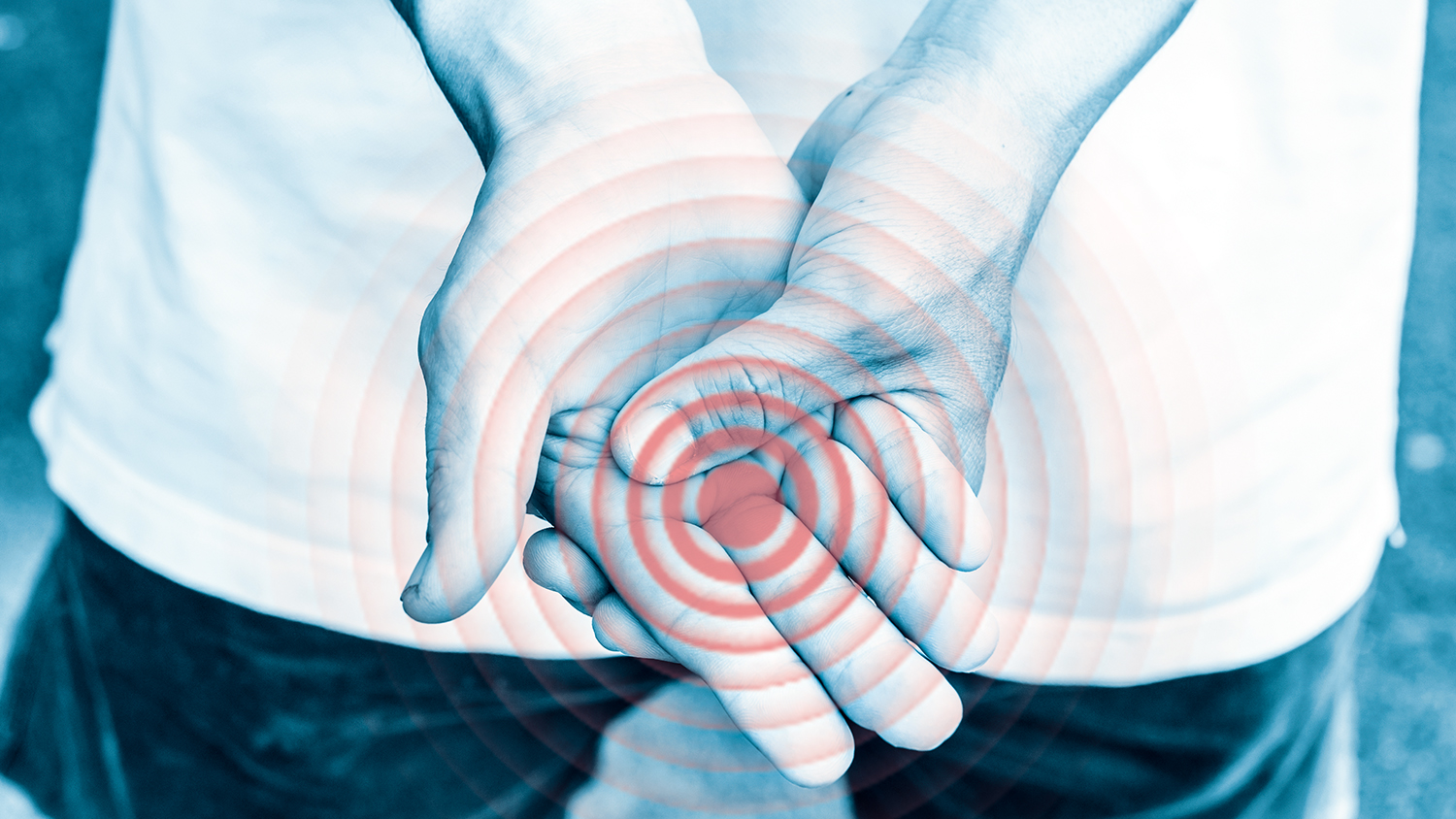
The HSE estimates that over two million workers are at risk of hand-arm vibration syndrome. This CPD explains how to manage the risks, with reference to a recent HS2 project.
Hand-arm vibration Syndrome (HAVS) is a health condition caused by the vibration from any handheld or guided power tools and machinery on site, such as drills, torque wrenches and plate compactors.
What you will learn in this CPD
- What hand-arm vibration syndrome (HAVS) is
- The legislation that protects workers from HAVS risks
- How HS2 included HAVS in its health and safety strategy
HAVS causes damage to muscles, nerves, joints and blood vessels, leading to permanent long-term health conditions. HAVS can cause vibration white finger – a permanent and painful numbness and tingling in the hands and arms – as well as painful joints and muscle weakening. There is also evidence that it may cause carpal tunnel syndrome.
HAVS can be prevented, but once the damage is done it is permanent. Regular or frequent exposure to hand-arm vibration is likely to occur when the use of vibrating tools is a regular part of someone’s job.
Over two million people in the utility and construction sectors in the UK are at risk of developing an HAVS-related condition, according to the Health & Safety Executive (HSE).
Each year, over 80 instances of HAVS are reported to the HSE as a RIDDOR (Reportable Injuries, Diseases and Dangerous Occurrences Regulations) reportable disease, under regulation of the RIDDOR Regulations 2013.
The Control of Vibration at Work Regulations 2005 aim to protect workers from risks to health from vibration. The regulations introduce action and limit values for hand-arm and whole-body vibration. These are:
- Exposure action value of 2.5m/s2 A(8): at this level employers should introduce technical and organisational measures to reduce exposure.
- Exposure limit value of 5.0m/s2 A(8): this should not be exceeded.
HSE provides a list of alternative processes to avoid or reduce the use of vibrating equipment in construction.
These include:
- mechanised tunnelling methods, to eliminate hand digging;
- use of machine-mounted equipment such as breakers and crushers instead of hand-operated tools for groundworks and demolition; and
- designing and planning to avoid the use of masonry drilling.
HSE describes as “not acceptable” the use of hand-operated tools for pile-capping and scabbling. Instead, it recommends alternative methods where technically appropriate, such as suspended hydraulic pile croppers, grit blasting (wet or dry)
or the Elliott method, among others.
HSE also provides guidance on management of HAV risks where use of vibrating equipment is unavoidable, which includes better selection of work equipment, limiting daily exposure time, improving information, instruction and training, and health surveillance.
HSE states that “where a risk cannot be eliminated an employer needs to reduce the exposure to as low a level as is reasonably practicable through organisational and technical measures”.
HS2 HAVS risk
On HS2, HAVS was identified as one of the top occupational health concerns in its health and safety strategy.
The condition came into focus during the EKFB (Eiffage, Kier, Ferrovial and BAM) JV’s construction of the A41 onsite batching plant near Aylesbury in Buckinghamshire.
“Often on site a power tool will be used in conjunction with another static metal tool such as a spanner, for example when tightening bolts to erect a scaffolding tower or metal structure,” explains Timothy Callow, safety, health and wellbeing advisor with EKFB. “In these situations, the vibration source is coming from the power tool but is transferred through to the static metal tool and to the operator’s hand.
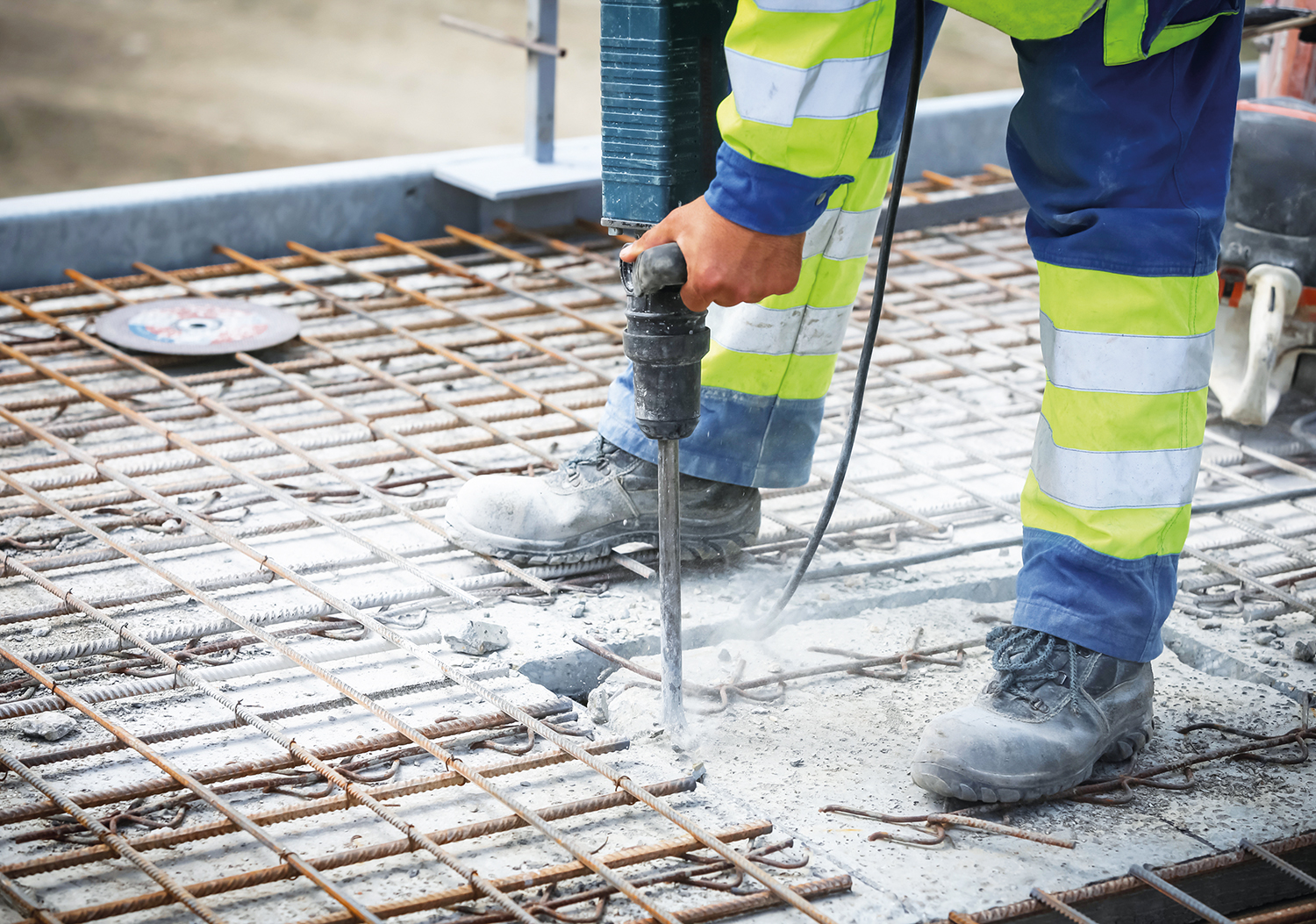
“On the batching plant, there was a need for thousands of bolts to be manually inserted. These bolts had to be tightened with a metal spanner and a battery-operated torque wrench which produced vibration. More than 2,500 bolts were needed, potentially exposing workers to regular and excessive vibration. Tests showed that the vibration levels were double the upper value exposure level.”
Concerned that its contractor’s operatives were potentially being exposed to HAVS, EKFB asked for further support from its occupational health provider People Asset Management (PAM) to measure the HAVS exposure level and suggest ways of removing or reducing the exposure.
PAM provided an occupational hygienist and tests were carried out on the operatives to find out the exposure levels.
Occupational health assessment
The occupational hygienist used a professional HAVS meter manufactured by Pulsar connected to the spanner.
“The tests showed that the vibration levels in the hand holding the spanner (left hand) had an increased vibration exposure compared to the hand holding the vibrating torque wrench,” says Callow.
The exposure levels measured were double the HSE’s accepted HAVS upper exposure value level of 5m/s2 when tightening the support frame bolts (10m/s2), so there was
an immediate need to remove or reduce the risk to workers.
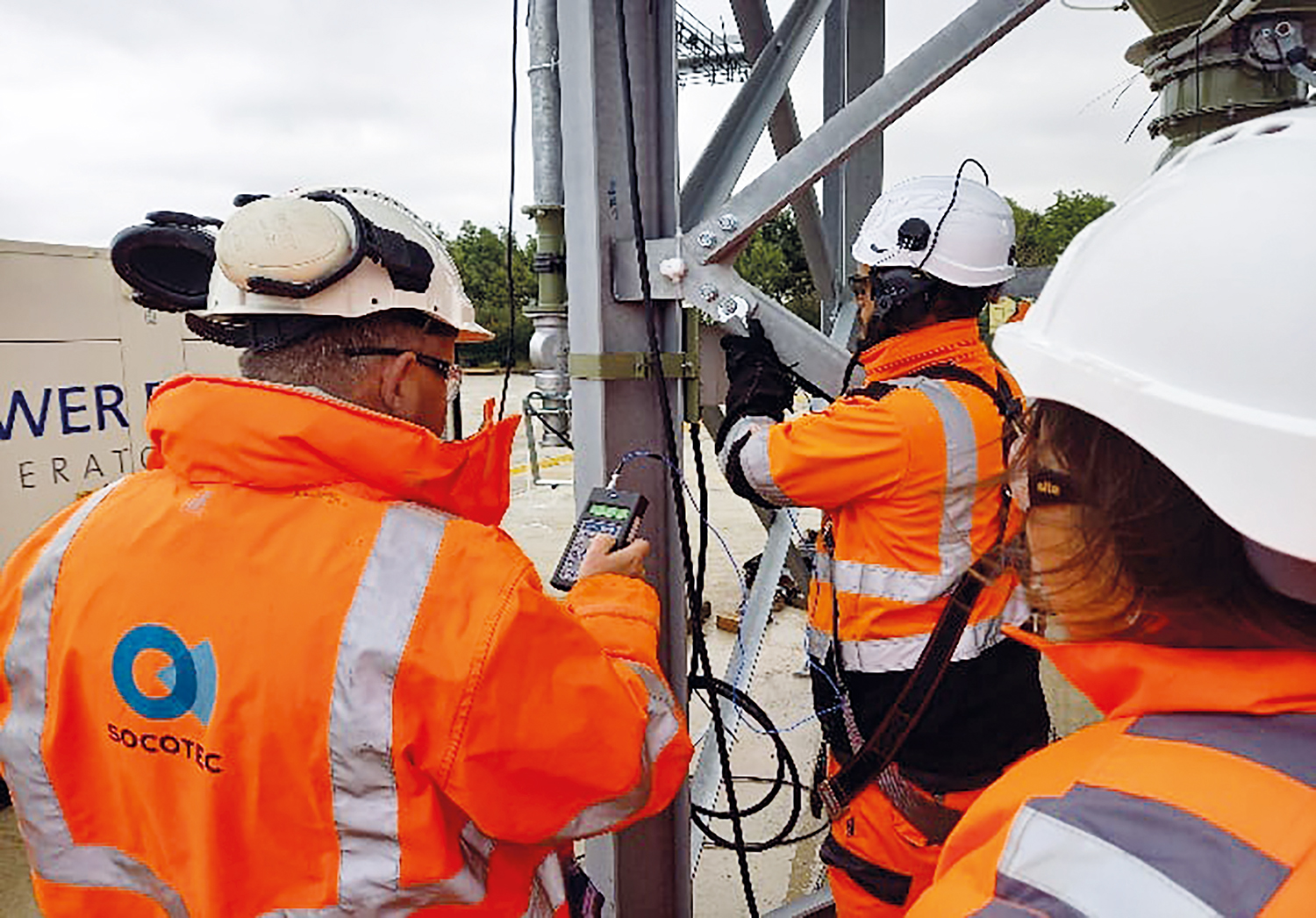
Data from HS2 HAVS tests on Aylesbury batching plant
EKFB carried out tests on workers using spanners with and without the rubberised insulated sleeve. The results were as follows:
Spanner without protection:
X = 3.80, Y = 6.35, Z = 6.74
Overall = 10m/s2 (double the upper exposure value limit)
Spanner with protection:
X = 0.37, Y = 0.19, Z = 0.23
Overall = 0.48m/s2 (reducing exposure to 5% of that without the added protection)
(X axis = forward/back, Y axis = up/down, Z axis = side to side)
A simple and cost-effective solution in the form of a rubberised/insulated sleeve was added to the spanner handle, costing approximately £1.50 per spanner, to see if this would reduce vibration exposure since there was no design solution available.
“This idea was derived from the collected experience of the people involved on site and the knowledge that some tools, such as hammers, often come supplied with a ready-made rubberised sleeve,” says Callow. “The added sleeve did not restrict work from carrying on normally.”
After adding the rubberised and insulated sleeve to the spanner handle, the results of the tests with the additional protection showed that the vibrations then being received were only one-twentieth, or 5%, of those without the additional protection – 10m/s2 unprotected down to 0.48m/s2 protected.
Learnings and recommendations
“HAVS is a major health risk on most construction sites. However, because its effects are initially hidden and longer-term, it can be easily overlooked or ignored,” says Callow.
“The potential HAVS risks on the A41 batching plant were more obvious because of the volume and intensity of the task over a period of 38 days.
“The project manager of the batching plant contractor agreed to use the new method on the erection of the remainder of the A41 batching plant and to adopt it on erection of a further batching plant on another EKFB site. They also confirmed that this method would be used on its future projects worldwide.”
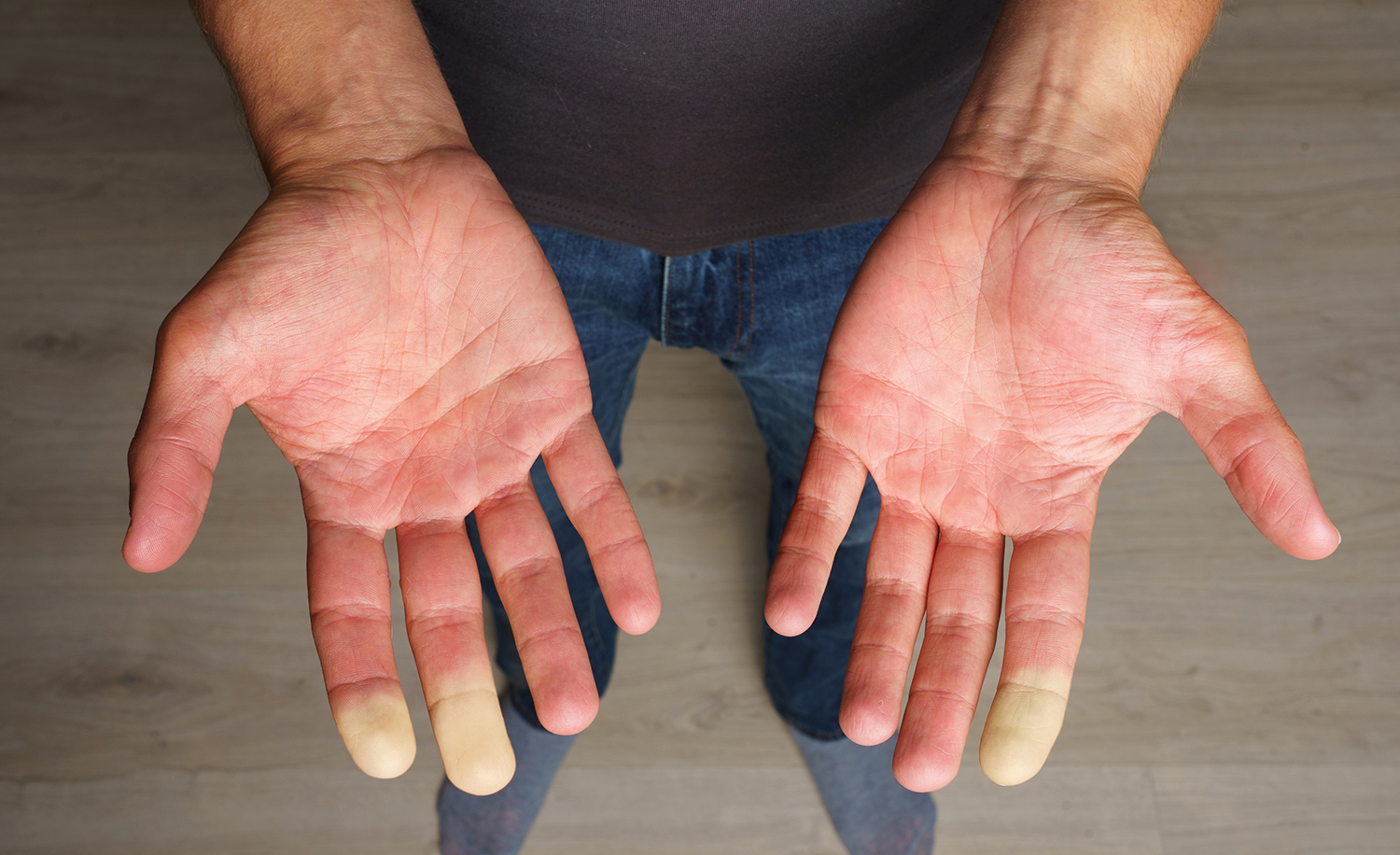
He adds: “The adding of a rubberised sleeve to a static metal tool has many more applications on site – for example, when erecting scaffolding or metal structures and in the erection of large plant, such as cranes, or in the repair of plant and machinery on site. These activities typically involve a large number of people on site – labourers, fitters, pipelayers, erectors – who represent 24% of the total HS2 workforce, some 7,200 people.
“This initial learning event has raised awareness of HAVS across EKFB’s Aylesbury area. EKFB has also produced HAVS support materials to use at inductions and HAVS medical assessments have been introduced for operatives.”
Useful resources
- Hand-arm vibration at work: www.hse.gov.uk/vibration
- The Control of Vibration at Work Regulations 2005: www.legislation.gov.uk
- Treatment for HAVS: www.patient.info
Additionally, Reactec’s HAVS monitoring system has been introduced on EKFB sites. The Reactec system allows the monitoring of daily HAVS exposure levels for all vibration tools being used on site for activities such as drilling, concrete trimming and scabbling, ensuring that the minimum exposure value level for each tool is not exceeded.
HS2 case study supplied by PAM and EKFB for the HS2 Learning Legacy library.