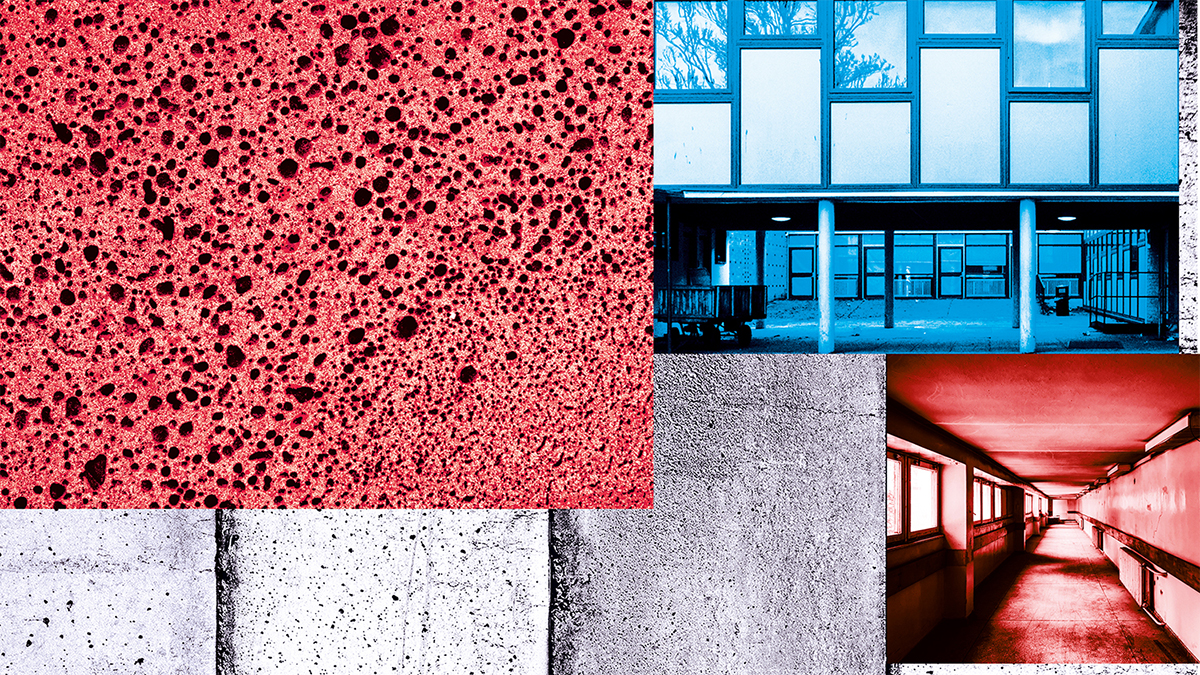
As an initial scramble to investigate the problem of RAAC in schools subsides, attention must turn to longer-term questions of how the industry mobilises to assess, monitor and manage vast quantities of the material installed in public and private sector buildings across the UK. Stephen Cousins reports.
Panic set in at the end of August when, just before the start of term, the Department for Education (DfE) decided to close over 100 schools in England in response to new concerns over reinforced autoclaved aerated concrete (RAAC), a lightweight concrete-like material that may be prone to collapse.
The abruptness of the decision was not only a shock to parents and teachers. Construction professionals were perplexed, given that the dangers of RAAC were already documented and the government itself had been warning about the potential for panels to collapse over a year before.
The lightweight concrete, with its bubbly fill material, was installed nationwide mostly between the 1950s and 1980s (see panel below). It can become a problem when risks are not picked up. These include the material being cut during building modifications, degrades in response to water ingress or overloading, and as a result of manufacturing defects, including end bearings that are too short.
As surveyors and structural engineers are scrambled to inspect schools and consider mitigation measures, attention must now turn to the sheer scale of the problem. An array of public and private sector buildings are likely to be affected as well as potentially hundreds of thousands of RAAC planks and panels used to build roofs, floors and walls across the UK.
RAAC is used across an array of building types. The number of buildings containing it is in the minority, but some hospitals, for example, have thousands of RAAC panels. The NHS in England started a £698m remediation programme in 2021.
New forms of assessment
RAAC now looks set to be treated as a building defect like asbestos or aluminium composite cladding.Living with it over the longer term will require more research into the material’s properties and related risks, developing new forms of assessment, monitoring and systems for mitigation.
Surveyors and engineers will need training to understand all the risks and identify appropriate remediation measures. Assessment could require specialist knowledge, given the sheer number of panels and the fact that signs of degradation may be concealed under the surface.
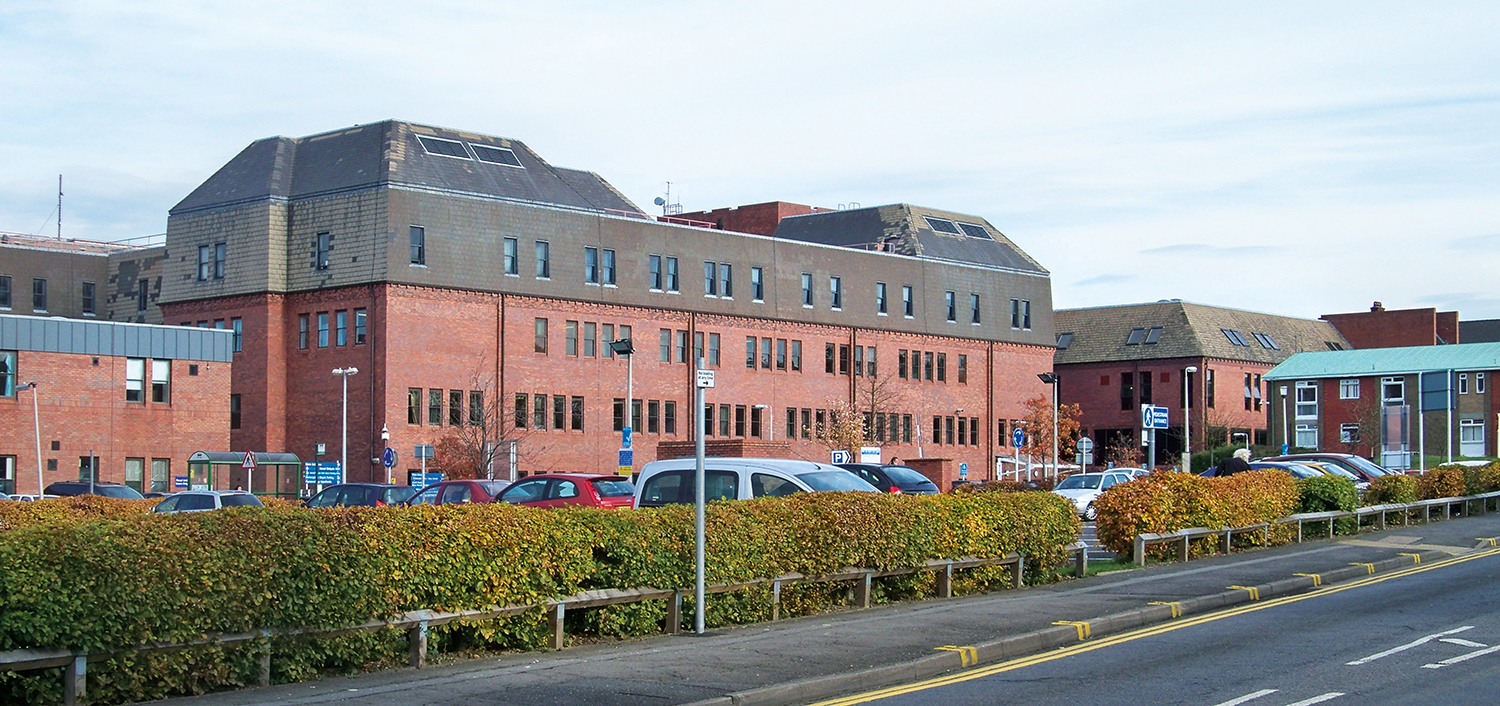
Tony Jones, technical director at the Concrete Centre, tells PSJ: “As an engineer, you’re never going to be able to examine every detail on every plank. You’re going to need to apply your engineering judgement regarding the amount of intrusive work you need to do and what is an appropriate remedial measure… It’s very hard to come up with a simple rule on risks associated with a failure at some point in the future. It will depend on what you find, which will vary from building to building, even from plank to plank.”
Schools ordered to close
RAAC cast a shadow over the start of the autumn term when 104 schools in England containing the aerated concrete were ordered to close by education secretary Gillian Keegan.
The closures were triggered by the sudden failure over the summer of three RAAC concrete planks – previously classified as non-critical. Keegan asked remaining schools across England to respond urgently to questionnaires stating if they had any of the material installed and, where it was confirmed, to keep those spaces out of use.
A total of 214 schools in England containing the concrete had been identified at the time of writing. The severity of the response from the Department for Education (DfE), and the associated costs and disruption, put a spotlight on RAAC in public buildings, from courts to military buildings to hospitals, and large private sector properties built before the turn of the millennium.
“There’s possibly not been a full understanding of the extent of RAAC within construction,” Patrick Hayes, technical director at the Institution of Structural Engineers (IStructE), tells PSJ. Although public sector clients have been aware of it for some time, private sector building owners have not until now had the “trigger” to become aware of its potential presence in their buildings, he adds.
IStructE has issued guidance on managing RAAC and set up a dedicated working study group, which was due at the time of writing to publish a desk-based study on the extent of RAAC in the private sector.
1960s and 1970s buildings
According to Hayes, the most common culprits are system build-type spaces put up in the 1960s and 1970s. These include supermarkets, airports, theatres and warehouses, which needed a lightweight material to create long-span roofs.
Concerns about RAAC date back to 1996 when a paper by the Building Research Establishment, on roof planks installed before 1980, warned of “excessive deflections and cracking”.
The matter rose up the agenda in 2019 when the Standing Committee on Structural Safety, the HSE, IStructE and ICE, issued a joint alert warning that pre-1980s RAAC planks had a useful expected service life of around 30 years before replacement should be considered. However a number of experts point out that, providing the material is properly checked and well maintained, it can go on for longer.
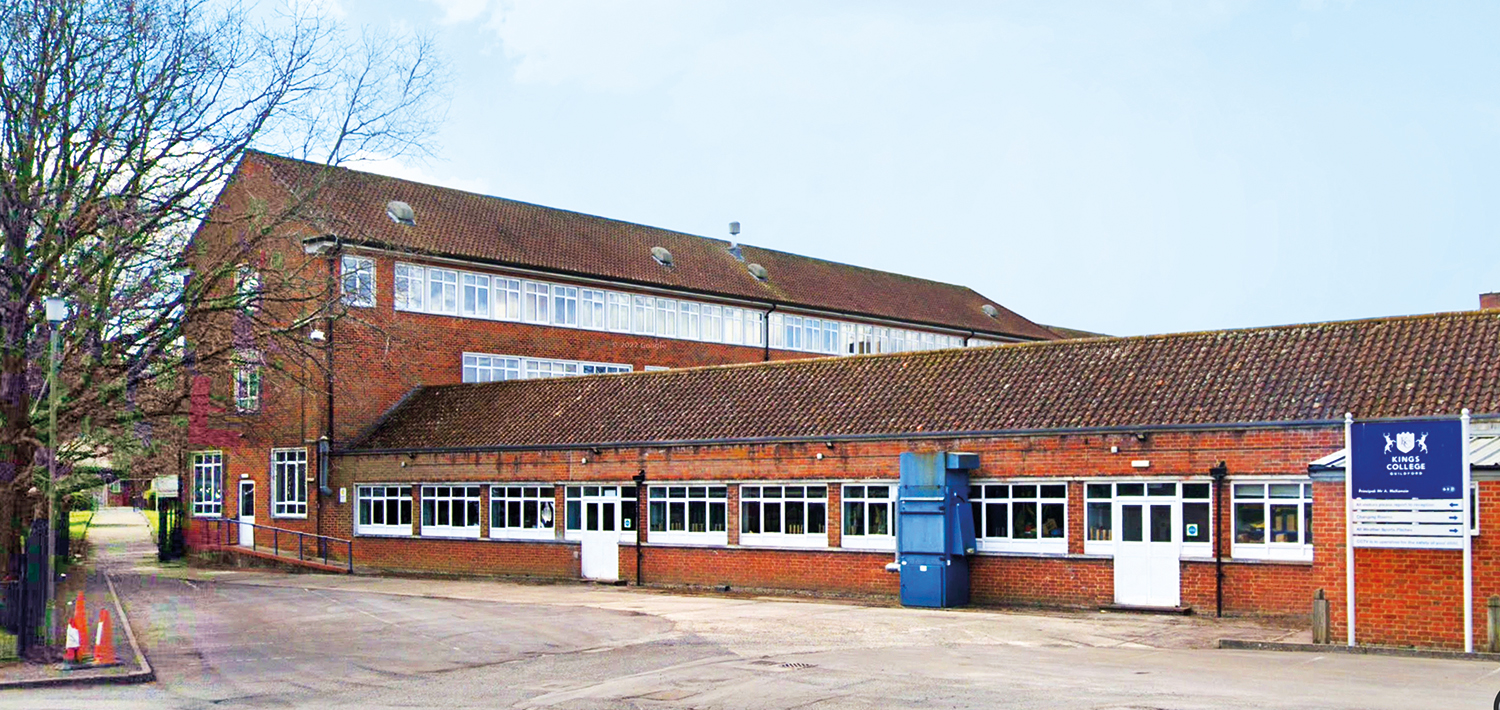
Chris Gorse, professor of construction management and engineering at Loughborough University, says that the presence of pre-1980s RAAC does not necessarily mean it is inherently dangerous and the structural risks may not demand a widespread programme of demolition or replacement.
Loughborough University is the only institution to research thoroughly the structural issues with RAAC. Gorse and his colleagues were part of a consortium, including engineer Sweco, materials specialist Lucideon, Concrete Preservation Technologies and digital specialist IAconnects, examining the concrete on behalf of the NHS in England to inform its remediation programme.
“The material is not inherently poor,” Gorse tells PSJ. ”As a lightweight aerated concrete with no coarse aggregates it has a relatively low compressive strength but, once the reinforcement is in place, in most cases it acts well as a beam and manages to transfer bending loads and shear stresses.”
Lifespan ‘not the deciding factor’
RICS guidance states that the widely reported ‘30 years’ lifespan of RAAC, “should not be the deciding factor” in decision-making, as it can last longer if the building is well maintained and the original design factors, such as calculated load weights, haven’t changed.
“Indeed, we’ve not found any evidence that RAAC was designed for a 30-year lifespan. The manufacturers’ technical literature that we have reviewed does not make reference to this short lifespan,” says Gorse.
“All of the beams that we have tested in the field and in the laboratory, some of which are 50 years old, have met or exceeded their original design strength. The main problem is with the bearing and ensuring that transverse reinforcement – reinforcement that spans the width of the concrete – sits over the bearing support.”
In many cases, a lack of proper asset management and building maintenance have led to RAAC being damaged. Much of the RAAC recently reported has been “abused, neglected and overloaded” over the years, says Gorse.
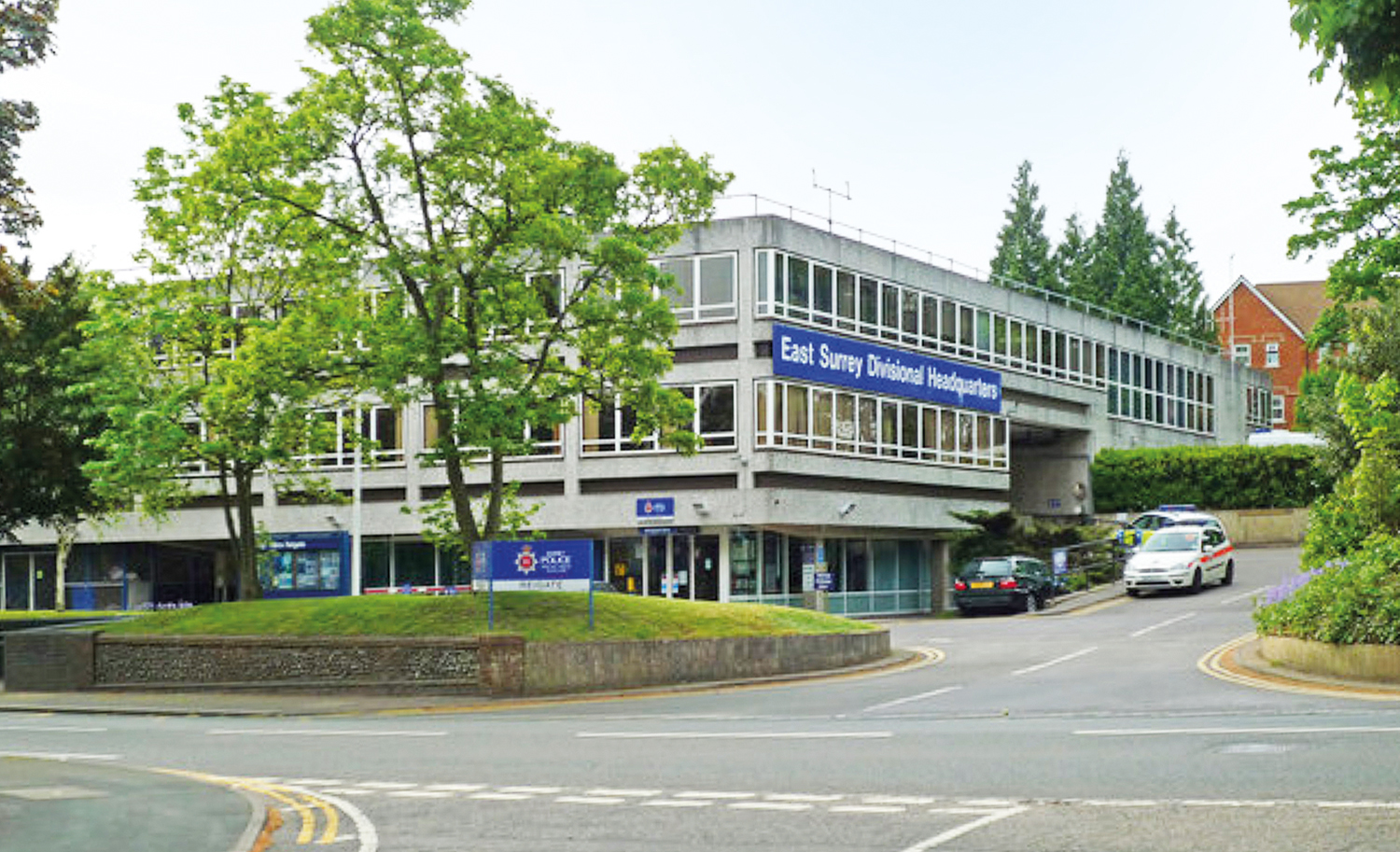
This has caused “excessive deflections” and “significant water ingress”, where rusting steel reinforcement has created spalling (breakdown of the concrete surface from the main body). Such deterioration is easily observed and remedial action should be taken.
Researchers found instances where panels were cut or pushed through building services, destabilising the concrete.
A “dangerous latent risk”, which has resulted in at least one outright failure and other instances of partial failure or collapse, relates to a lack of reinforcement embedded in the bearing ends of panels during manufacture.
RAAC panels are embedded with two layers of mesh reinforcement. Longitudinal bars span the length and transverse bars span the width, locking the longitudinal members in place and transferring forces into them. Aerated concrete is weak and the integrity and positioning of the reinforcement is crucial to its performance.
Rebar positioning varies
Transverse reinforcement is most critical at the bearing ends, where planks rest on either a wall or beam and the loads are greatest. In forensically taking buildings apart, Loughborough found that the position of rebar varied substantially and sometimes veered outside of the bearing area specified by the manufacturer.
In addition, variations in the way panels were constructed on site meant that while manufacturers often recommended that panels were positioned over a 40-50mm bearing area, in reality beams with as little as a 10-20mm bearing have been found. Such poor practice significantly increases the risk that transverse bars would miss the bearing location.
If RAAC is inspected and found to have been constructed and manufactured properly, then the research, at least the work done so far, does not suggest that RAAC poses a significant risk. This being said, a surprising number of cases have been found where the bearings and construction are not adequate and immediate action is necessary.
“Where panels and bearing have not been inspected, or RAAC has been found to have excessive deterioration, remedial supports are necessary to protect building users,” says Gorse.
New insights into the problems that can affect RAAC have shifted the goalposts in terms of how building owners and managers will need to assess and manage structures.
Jones comments: “Cases uncovered in the 1990s involved quite large deflections and cracks in planks so you had some idea before they failed that something was wrong. Now, we are starting to see another type of failure. If you have got RAAC you can’t just assume that because it looks alright it is OK. In most cases there will need to be an investigation.”
Inspection and risk assessment
Official guidance from IStructE and Collaborative Reporting for Safer Structures UK (CROSS-UK), suggests that, if the presence of RAAC is not known, the first thing to do is to ask a chartered surveyor or structural engineer to carry out an inspection and risk assessment.
If RAAC planks are uncovered, a chartered or incorporated structural engineer needs to determine their structural condition. The sheer number of buildings that will need investigation has raised concerns over the number of qualified professionals available.
A recent report by CROSS-UK uncovered a RAAC assessment carried out by people “who did not appear to have appropriate experience” and indicates that some schools may be engaging with the wrong people.
According to Hayes, a relatively small pool of around 24 chartered structural engineering companies have been carrying out RAAC investigations over the last two years. That number has since broadened. Both the RICS and IStructE have issued new guidance and are running training webinars on how to recognise RAAC and assess the risks.
“What we’re saying is that any chartered or incorporated engineer that is familiar with our guidance, in particular the webinars and training that we’re just putting out, should be able to identify it (RAAC) and recommend proposals,” says Hayes.
Delving deeper into specific remediation measures and rolling out a programme of related training will take longer, he adds, partly because more research needs to be carried out to understand the material’s behaviour.
This includes research into how RAAC performs on very narrow bearings and how to repair it without causing corrosion. It is difficult to bond the porous structure using current solutions. IStructE is developing performance specs for both temporary and longer-term propping systems.
Whole list of solutions
The solutions ultimately put in place will depend on factors such as the severity of the deterioration, the use of the space and the level of risk posed. “Given that we can’t wish RAAC away instantaneously, we’re going to need a whole list of solutions, rather than just one,” says Hayes.
The process could also be frustrated by the presence of asbestos within affected buildings built when asbestos was still legal to use, making it difficult to complete remedial works. According to the RICS, any remediation must take into account asbestos identification and requires careful management if it is present.
Refurbishment work is another area where awareness of RAAC is critical. IStructE is in discussions with the Construction Leadership Council about delivering an awareness campaign.
“A big risk area is when people drill or cut into RAAC – for example when they carry out roof works above it. So we really need to raise awareness among workers in building maintenance and refurbishment so they can identify RAAC and know how to work around it safely,” says Hayes.
Sudden failures of RAAC panels are very rare and typically result from intrusive work – such as outlined above. Whereas degradation tends to be a slow process that can be tracked, highlighting the need for longer-term monitoring and maintenance strategies.
The industry mostly relies on manual inspections and data analysis but this approach may be prohibitively slow and prone to mistakes. Greater reliance on photographic data, or other forms of survey or sensors, could provide a more accurate record or a secondary record for cross reference. AI and machine learning can be used to interrogate the photographic data and instantaneously spot any changes
Algorithm detection
Loughborough University has developed a computer algorithm able to detect and predict the occurrence of cracks in RAAC. The tool was trained on 85,220 images of concrete on NHS trust estates, of which 1,800 were RAAC, including timestamps of the pictures. The system was able to identify cracks in RAAC with an accuracy level of 95.8%. The plan is to integrate the tool within the survey processes of NHS trusts’ estate teams.
“We need an early warning that something in a roof, floor or wall beam is changing and we need to do something about it,” says Gorse. “This is where machine learning and AI comes into its own. It can recognise things that people wouldn’t recognise. it works as a really effective backup when you’ve got huge quantities of data.”
The many strands to the RAAC phenomenon make it difficult to predict how the industry’s response will play out over the coming months and years. But what is clear is the substantial costs and manpower required.
Building owners and managers clearly need a stronger understanding of RAAC and other materials within their buildings, to enable them to form a more detailed picture of the risks and how to control them.
What is reinforced autoclaved aerated concrete (RAAC)?
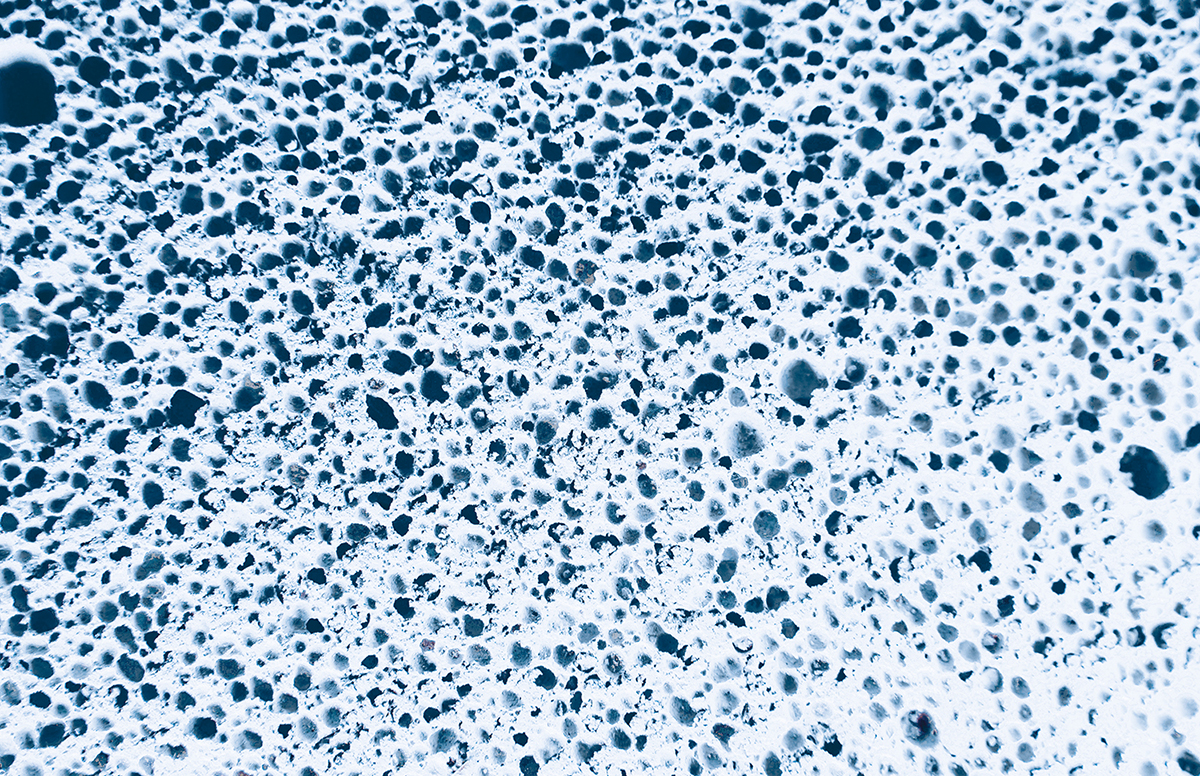
RAAC is a reinforced lightweight concrete formed into panels or planks. Unlike regular concrete, it contains no coarse aggregates. Instead a mix of fine aggregates and chemicals creates gas bubbles to increase its volume.
It is not as strong as concrete in compression and requires steel reinforcement to boost its strength. Because rebar does not bond well with the aerated material, transverse bars are needed to lock the longitudinal bars into place.
Compared with traditional concrete RAAC is a ‘softer’ material and as such can be easily penetrated, explains Chris Gorse, professor of construction management and engineering at Loughborough University.
RAAC was mainly used in flat roofs and in some floor and wall panel construction in the UK between the mid-1950s and mid-1990s. It was not installed in significant quantities after 1980.
It is thought to be more common in schools, hospitals and public buildings and has been discovered in theatres, courts, sports halls, public toilets and other non-domestic buildings.