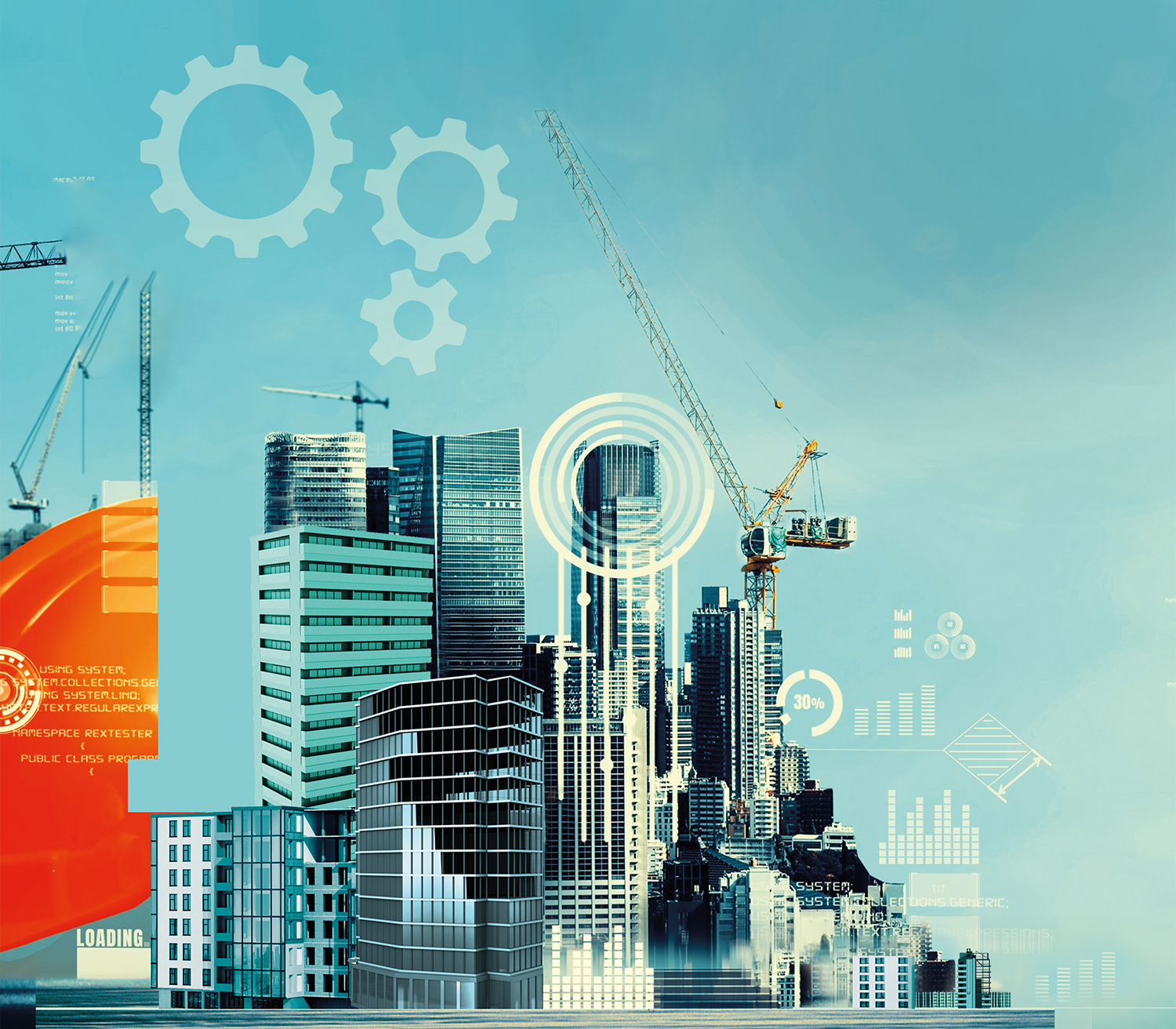
Contractors are looking to new technology to provide simple, cost-effective solutions that are already making construction sites safer places to work. Here, Denise Chevin introduces a selection of innovations we’re likely to be seeing more of.
From remote flying drones to Spot-the-dog robots to exoskeleton suits to immersive virtual reality headsets, construction is awash with new technologies with high aspirations to make the industry more efficient and safer.
There is no question that if workers can be removed from harm’s way then the risks are reduced. But while some of these technologies will be able to take workers out the equation in time, for the most part they are either in the developmental stages – a little clunky or gimmicky, or cost- and skills-wise still outside the realm of many construction projects. We may have to wait some time before robots lay bricks and self-driving excavators are the norm on site.
But those looking to make construction a safer place today are also looking to digital methodology to provide simple and cost-effective solutions that can be easily embedded into construction workflows. Here we speak to contractors and health and specialists to find out more about some of the innovations we could be hearing more of in 2023.
Seeing is understanding
ISG introduces a visual approach to site safety.
“Many different technologies are emerging that are potentially seen as being able to improve safety. There are those like robot dogs or laser-guided diggers – technologies like that, which reduce the need of someone to do the work. But that’s not always possible or practical and they don’t necessarily add anything different to what we’ve had before,” says Andrew Hughes, director of health and safety at ISG.
“And there’s the big-data approach where you collect more data and then use that in a way to predict where situations might be riskier. But to a certain extent it is still guesswork.
“ISG wanted to take a different route – one of getting close to the actual work and looking at how we can reduce risk,” he adds.
RAMS visualisations
One of the ways ISG is doing this is in the production of visual standards for sites to enhance engagement and compliance. A particular element is around visualising risk and method statements (RAMS).
ISG is working with several supply chain partners to use these RAMS visualisations (either static images or videos) in daily site meetings to show key activities.
Hughes explains that it means personnel can now see rather than just hear about activities – and also understand the correct procedures through the visual medium.
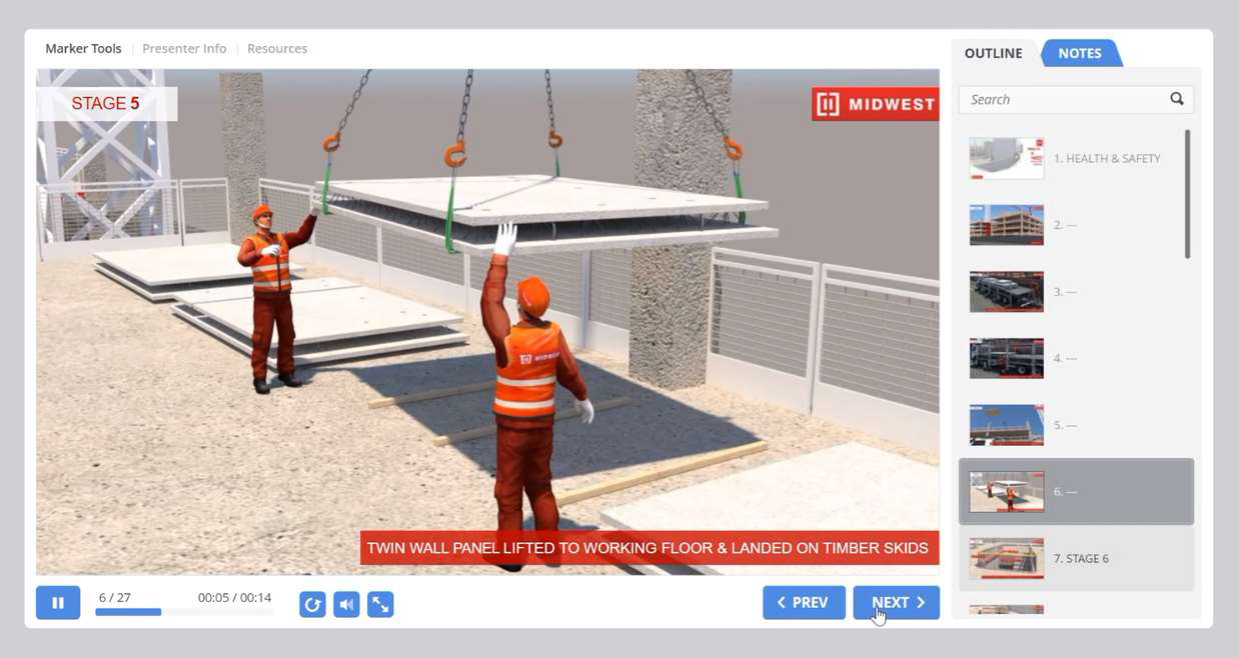
He says: “It might be about turning your method statement into a short video that people can grasp and see and understand very easily. Or it might be using modelling software that you can get off the internet, or it might just be some sort of animation.
“We felt there was opportunity there, using those visualisations, to say this gets us to a better understanding of what are sometimes very technical types of work – and where those risks are and how those things will be mitigated.”
ISG has worked with suppliers to produce the visualisations – some suppliers have included voiceovers in several different languages – to set out procedures for tricky activities such as working at height using mobile elevated platforms or installation of ventilation systems.
“We’re augmenting this content with short video captures from our site team to chart day-to-day logistical changes, so we’re showing rather than telling delivery teams about important updates. It’s about bringing people closer, stimulating conversations and working through challenges together and bringing RAMS documentation to life, so everyone understands what the correct methods look like.”
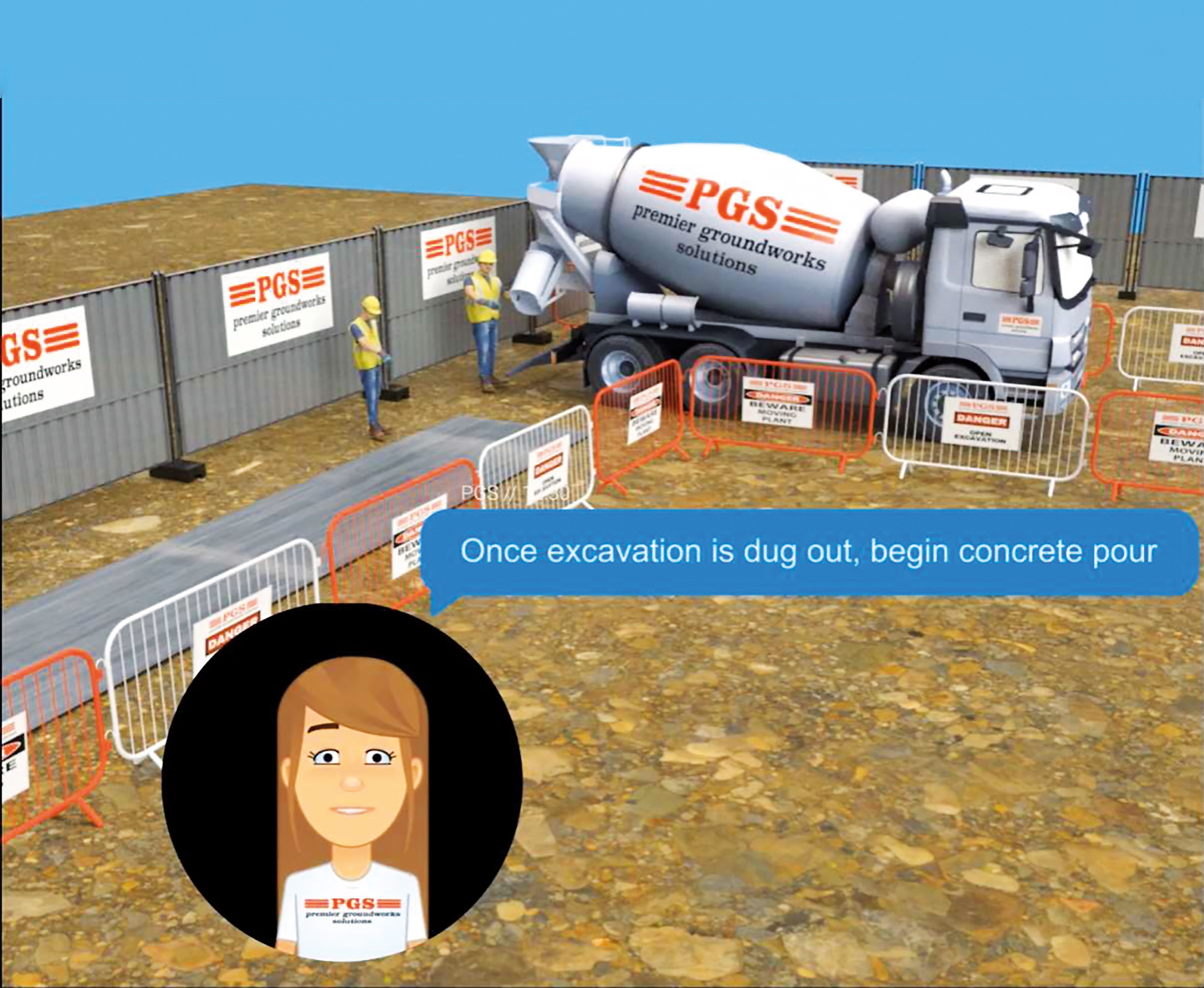
ISG says that feedback from suppliers on the visual RAMS is that they see this can be quickly implemented across the industry – it’s also helping them unlock the talent they already have in their teams around digitalisation and challenging traditional methodologies. The idea he says would be that it would be inexpensive and easy to put together.
Hughes says the visualised method statements have rolled out across the business in Wales and they are working out which technologies work best, with the plan to use them more widely in the future. “We have other systems that this can potentially interact with. There is a move towards OpenSpace – this is a system that uses a standard 360-degree camera attached to a hard hat that passively records images as a builder walks the site carrying out their duties,” he says.
“The image data is uploaded to the cloud, where algorithms automatically map the photos to project plans and ‘stitch’ them together to create an accurate visual representation of the site without any human intervention.”
Risk library alerts of design dangers
Software allows risk to be designed out before site work begins.
A key emphasis on improving health and safety across construction is designing out risk in the first place. This is very much the theme of a programme of work funded through the Lloyd’s Register Foundation’s Discovering Safety Programme and delivered by the HSE, industry partners and academics at the University of Manchester.
The Construction Risk Library project is a highly important piece of work – an award-winning programme that started in 2019. The HSE’s Gordon Crick is technical lead on the project, which is about to start its third phase. The HSE team has been working closely with Dr William Collinge, lead investigator in the Thomas Ashton Institute, University of Manchester.
The library builds on the developing trend of using 3D and 4D models that allow planners to represent visually how a construction plan is sequenced before it starts on site. It brings an additional dimension, says Crick: “What we’re trying to do is to make the models more valuable for health and safety by adding extra information about the risk and the context of the risks.”
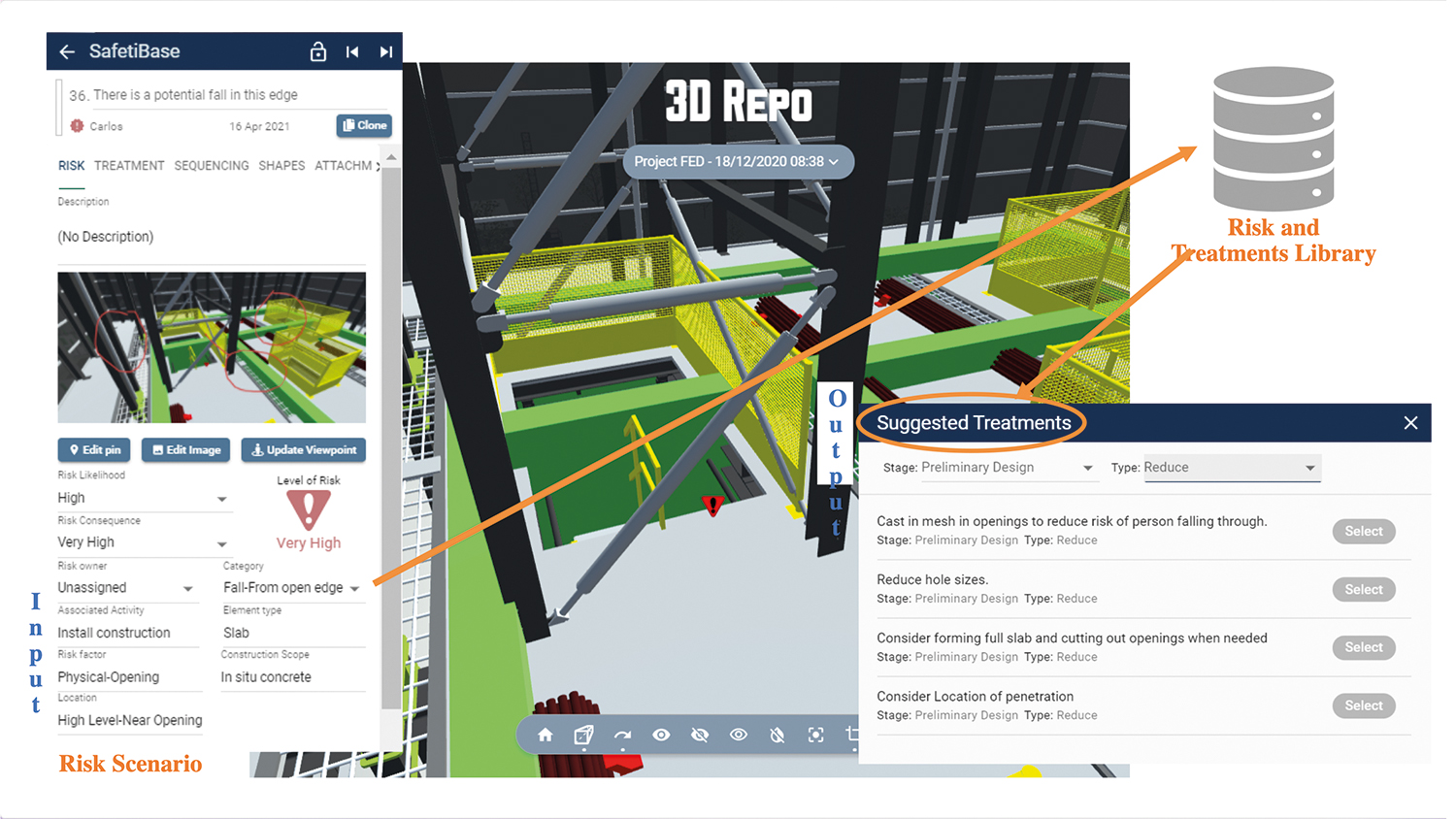
Crick says the team has gathered information on risks, including analysing hundreds of HSE press releases of incidents. Common risks are then tagged in a software tool that can be linked to the models. The software can be searched, with risks flagged up on screen when a scenario involving the risk is depicted. The software contains data about the risk and potential solutions for mitigating it.
There are about 300 risk scenarios in the library. The team is looking to grow this with help from those in the industry who can supply data and risk scenarios which are then anonymised.
The library is embedded into a tool called SafetiBase, created by software firm 3D Repo with industry partners including Atkins, Mott MacDonald, Laing O’Rourke, Costain, Bentley, HS2 and Tideway. The development of SafetiBase was funded by i3p and Innovate UK.
Safetibase is open source software which, as well as allowing users to mark up risks within a model, enables them to complete various information fields and apply the risk rating, which can be updated if changes are made.
“It’s much more a visual, immersive, digital way of mitigating health and safety risks that can be shared.”
Safetibase is compliant with PAS1192-6. Although it can be used in conjunction with 3D Repo’s BIM model viewer, it uses a common schema which means that it can be used with any BIM model. To date, the library has been piloted on a number of projects with organisations such as AstraZeneca, Atkins and Multiplex.
Says Crick: “It also works well as a collaboration tool. A contractor could identify a problem on site, take a photograph and send to an architect or an engineer, enabling them to share the problem instantly and discuss a solution.”
Manchester University’s Collinge says of the work: “It’s exciting and groundbreaking. It’s much more a visual, immersive, digital way of mitigating health and safety risks that can be shared collaboratively from architects or contractor to whoever is involved.
“The other exciting thing is the data. The library is in effect a vast collection of data. So the idea is this library grows and grows over time, with data from various projects. And so it matures and evolves and becomes a generalised repository of data that is useful for any kind of project to interrogate.
He adds: “The tool also supports the new ISO standards for health and safety. So it really ticks all the boxes.”
While the Construction Risk Library concentrates on the design phase, another strand of the Discovering Safety work by the HSE and the University of Manchester is moving into the construction phase and trying to come up with leading indicators that can pinpoint health and safety risks using cutting-edge data analytics and AI.
Steve Naylor, senior scientist in HSE’s Science and Research Centre and a technical lead, explains: “One of the things we are interested in doing is assigning risk scores to projects and as part of that looking at how such risk indicators can be predicted.”
Balfour Beatty’s smartphone observation app
Employees can report observations of close calls.
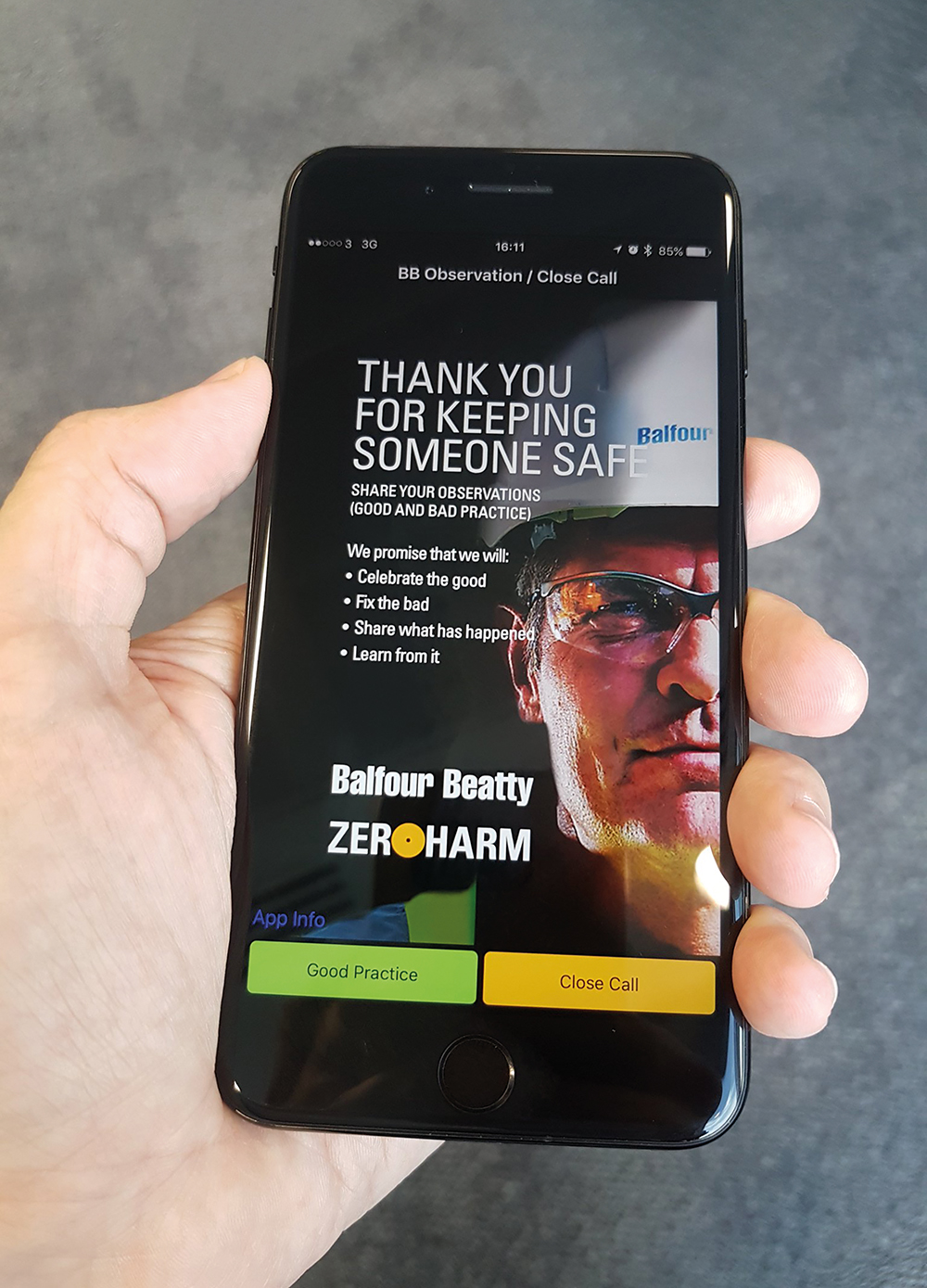
Sharing and learning is a mantra that’s well established in site safety – but how can you make this easy for all?
Balfour Beatty has come up with the Balfour Beatty Observations app to allow employees and contractors to report their observations of close calls and share best practice.
“The app provides an easy, anonymous method of reporting near misses in real time. It records the exact location of the reporter and captures photographic evidence of the incident.
“It can be used to simplify near-miss reporting and enable a greater understanding of the incident through the provision of photographic evidence,” says Balfour Beatty.
Safe distancing post Covid
Zonr smart safety system alerts workers to hazards.
In the days of Covid-19, firms turned to wearable alarms that alerted those on site if they were working too close to a colleague. Now one of the leaders in supplying this technology has widened its application to help prevent accidents in potentially hazardous situations.
Pathfindr, an asset tracking and industrial IoT tech specialist, has developed a smart safety system called Zonr. This is a proximity alarm that alerts workers when a vehicle or other hazard comes close, or if they step into a high-risk area, helping them to avoid potential incidents. It is a development of Pathfindr’s Safe Distancing Assistant, a wearable device to support social distancing launched amid the outbreak of the covid-19 pandemic in 2020.
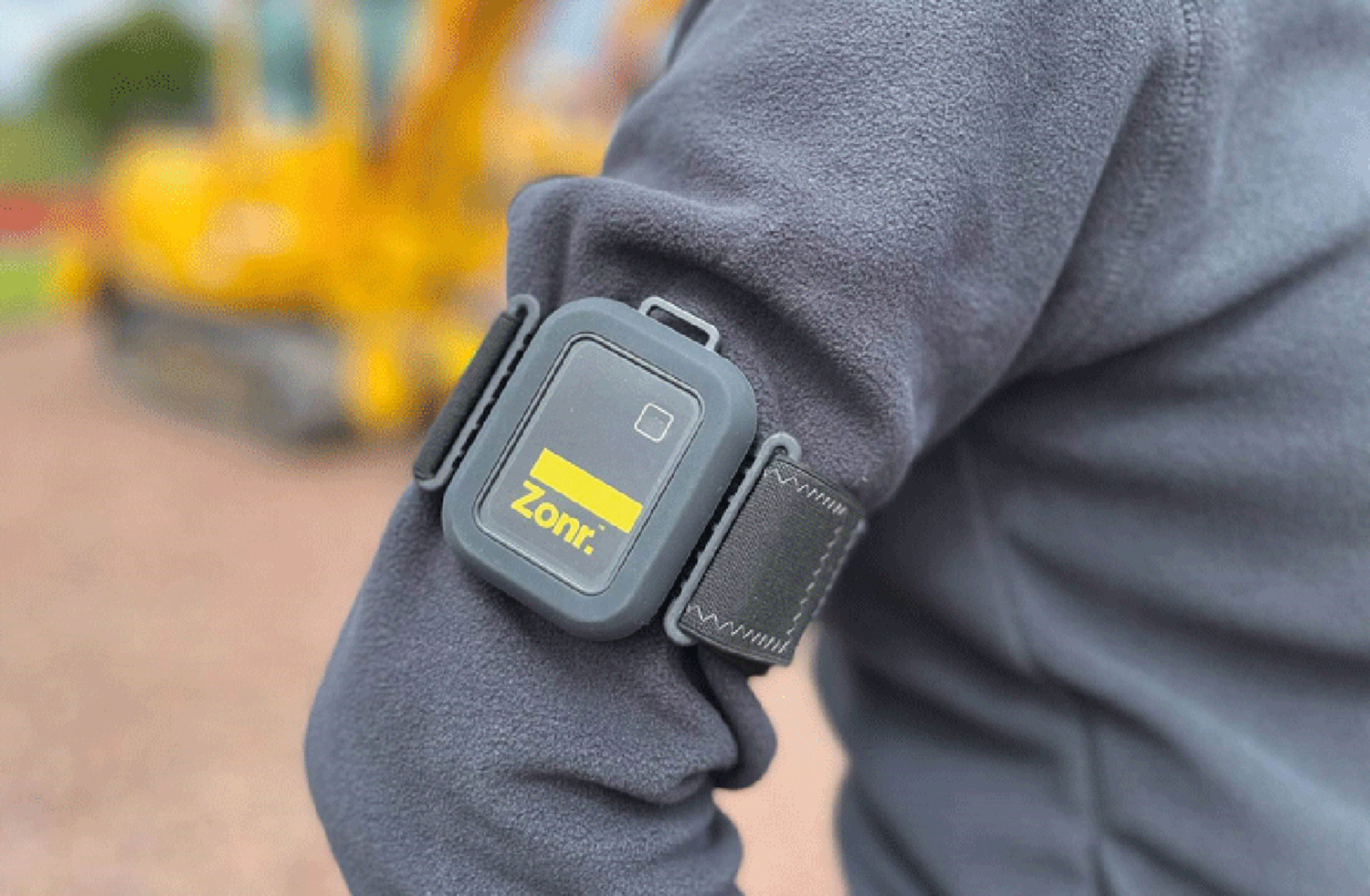
Zonr relies on a combination of GPS tracking and ultra-wideband technology to locate workers and hazards and create a dynamic virtual barrier – or exclusion zone – around those hazards.
The exclusion zone is created through signals sent between sensors – which can be placed anywhere within a site – and a control unit. The control unit alerts the plant operator to any incursion and also lets workers themselves know when they have entered an unsafe zone through a sounded alarm on a wearable device.
All set-up is completed through a mobile app and incursion data is viewed in real time via a web-based portal – with data transmitted to the cloud via a 5G connection.
“It’s certainly not a replacement for common sense. In effect it’s a nudge to say: look, you’re getting too close.”
The system gives site operators real-time data over incursions, enabling interventions to be made in the moment, as well as providing holistic data to enable overall health and safety processes to be improved.
It has been adopted by the rail contractor QTS Group, following successful trials. The company is now talking to a number of tier 1 contractors, says Andrew Scheer, Pathfindr’s marketing director.
He says that a major benefit of the system is that it also allows the management team – whether at site level, regional or national – the information really to investigate if there are any issues.
“It’s certainly not a replacement for common sense. This is an extra tool. In effect it’s a nudge to say: look, you’re getting too close to something that could be dangerous. And you’re letting the operator know that there is someone getting too close.”
Low-cost apps help shore up safely
Tilbury Douglas trials mobile apps on tank refurbishment.
Photogrammetry – the process of taking many photographs of an object from a variety of angles and stitching them together using algorithms to create a 3D model – has been making waves in construction. But the kit typically needed to capture such imagery – such as specialist cameras, or drones with LiDAR for example – can be expensive and needs experts to set up and operate. (LiDAR is an acronym of laser imaging, detection and ranging. It is sometimes called 3D laser scanning.)
Ben Bennett, principal engineer and head of temporary works at Tilbury Douglas, is trialling inexpensive mobile apps used in the animation industry to do a similar job, while producing centimetre-level accuracy as opposed to millimetre accuracy you might get with more expensive equipment, which is often adequate for communicating scenarios on site.
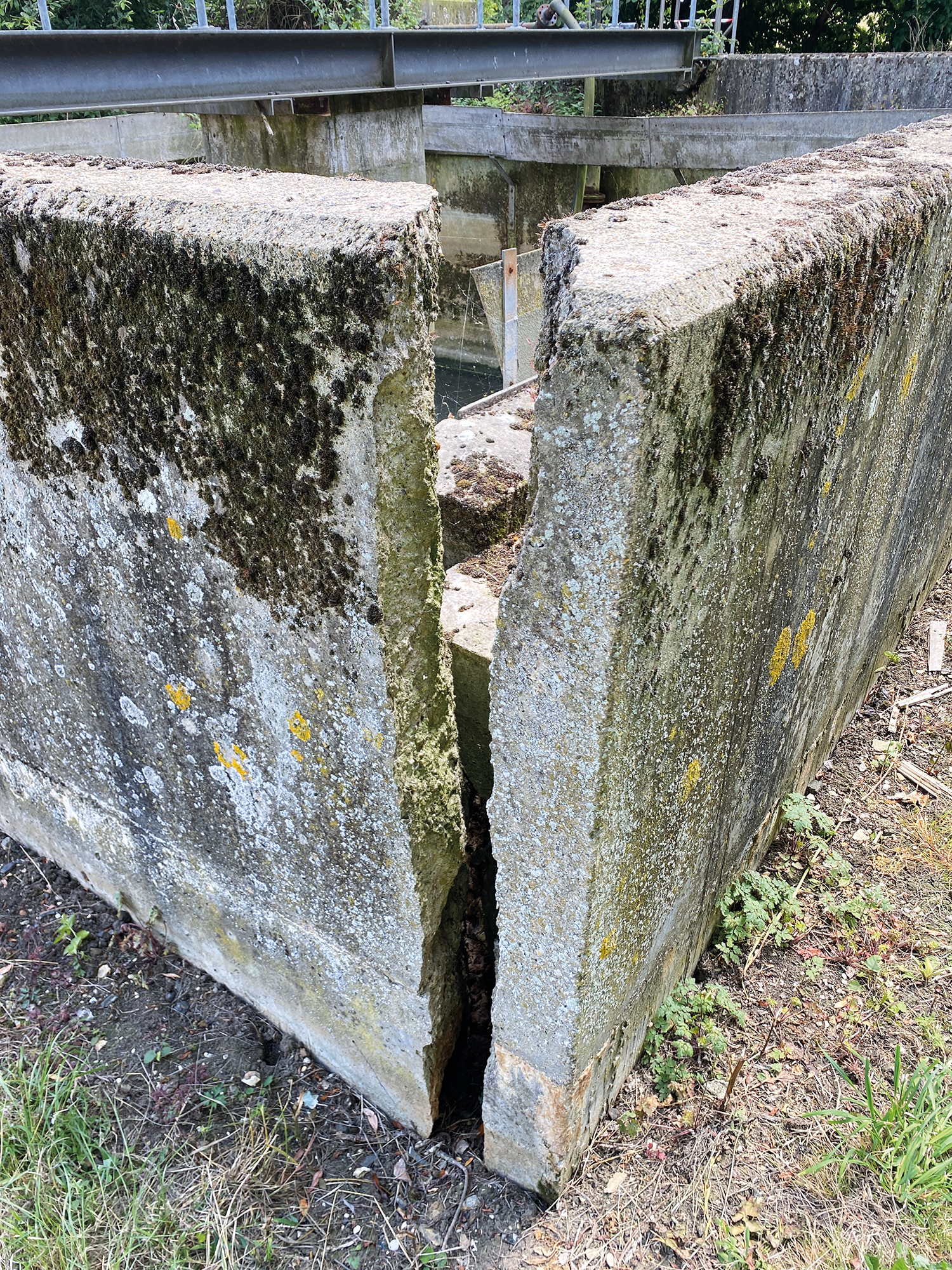
Tilbury Douglas is trialling two apps – Polycam and Metascan – on the refurbishment of a water tank for Thames Water (pictured left). Both are available on Android and Apple devices.
“If you need to react to something quickly on site, it is about speeding up that transfer of information to make sure we’ve got a suitable and safe design in place quickly,” says Bennett.
“So for example, where there is a need for temporary propping, it can sometimes be difficult to communicate the geometry with photographs alone. These apps allow anyone with a smartphone to produce 3D visualisations that can be shared with a designer remotely in a matter of minutes to help communicate the requirements. It may also make it easier to spot structural elements that might have been missed in a photograph and should help to establish a safer solution faster.”
The team is currently trialling the apps to help in planning the safe demolition of a large primary settlement tank for Thames Water. The virtual model, which users can ‘walk around’, was produced with the Polycam app using an iPhone.
“There is whole plethora of new technology and we are currently investigating many areas, such as virtual reality and augmented reality for instance, to improve safety on site,” adds Bennett.
“The industry is pushing for an adoption of new technology and digitisation, to catch up with other industries that have already embraced it for the better. We’ve got to continue to innovate and explore new technologies like this to keep up with the pace of change and improve efficiencies and the levels of safety we can achieve on our sites.”