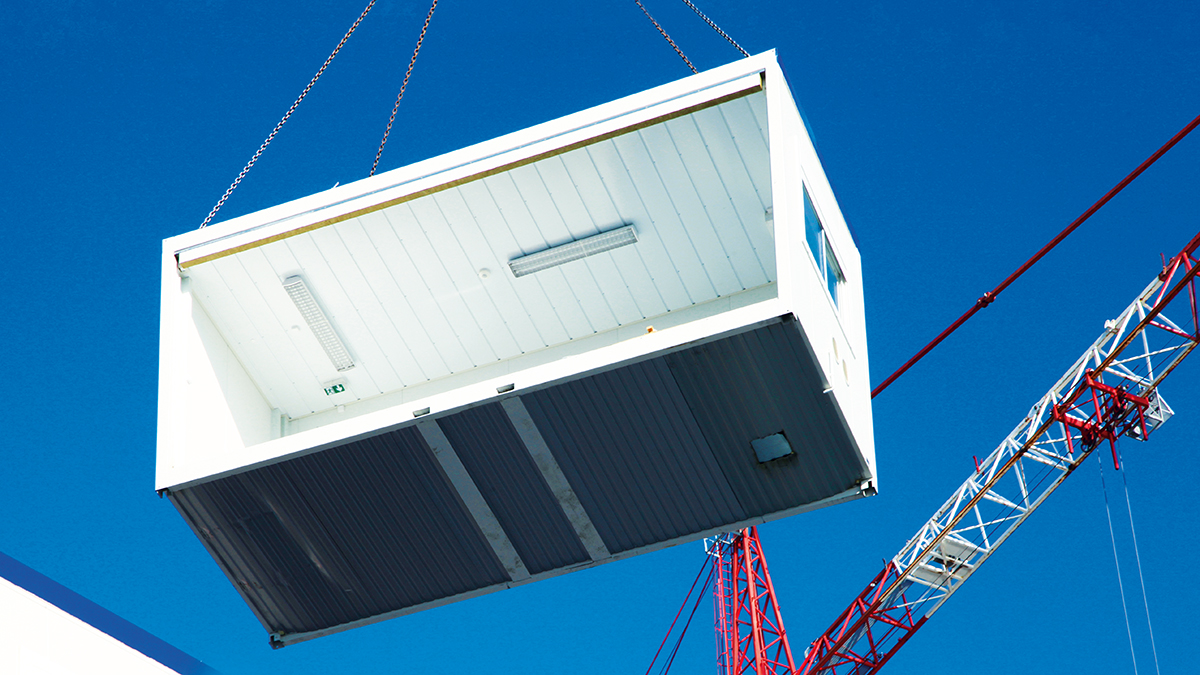
The demolition of five modular schools has raised questions over the safety of modern methods of construction. But with the right approach to design and risk management, offsite projects are able to deliver on innovation without compromising on build quality or worker safety. Stephen Cousins reports.
When the government unexpectedly forced schools in England to close in the summer due to the risk of collapse from reinforced autoclaved aerated concrete (RAAC) it rightly sent shockwaves across the nation. But the revelation masked another schools scandal which, though smaller in scale, arguably had equally serious implications for the education sector.
Just a couple of weeks after RAAC hit the headlines, it emerged that main buildings at two virtually brand new secondary schools and a primary school in England, all built using the latest modular, offsite construction methods, were being ordered to close with immediate effect.
Former schools minister Nick Gibb said issues with the structural integrity of the buildings, all constructed by the now defunct offsite contractor Caledonian Modular, prompted fears they would not be able to withstand extreme events, including severe weather or being hit by a vehicle.
Haygrove School in Bridgwater, Somerset, Sir Frederick Gibberd College in Harlow, Essex and Buckton Fields Primary School, near Northampton, have since been condemned to demolition. Earlier in 2023, two primary schools in Cornwall, only partly completed by Caledonian Modular when it fell into administration in March 2022, were completely demolished.
Spotlight on MMC
The Department for Education (DfE) commissioned the schools under its £3bn modular framework and has come under fire for allowing the failures, though it’s still unclear where the responsibilities lie for signing off the projects. It is reviewing contracts and taking legal advice on how to recover costs.
The Caledonian Modular problems, although isolated, throw an unexpected spotlight on modern methods of construction (MMC). MMC is normally considered a safer form of construction because moving work offsite to a factory should result in higher-quality buildings less likely to fail. It also limits operatives’ exposure to hazards on unpredictable building sites and requires less working from height.
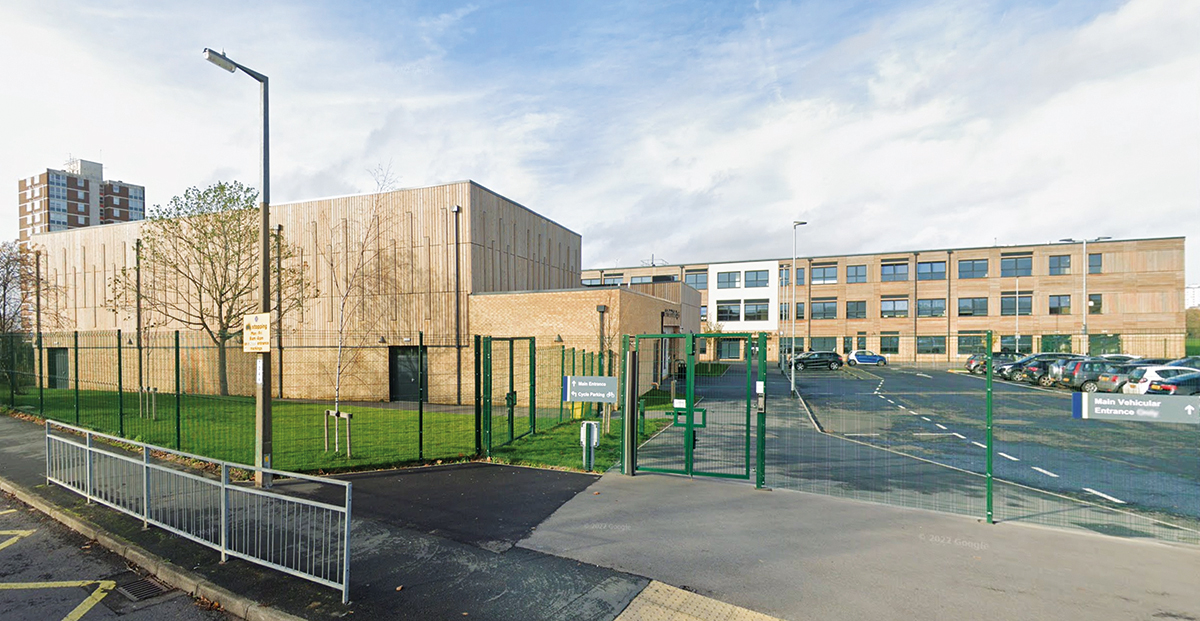
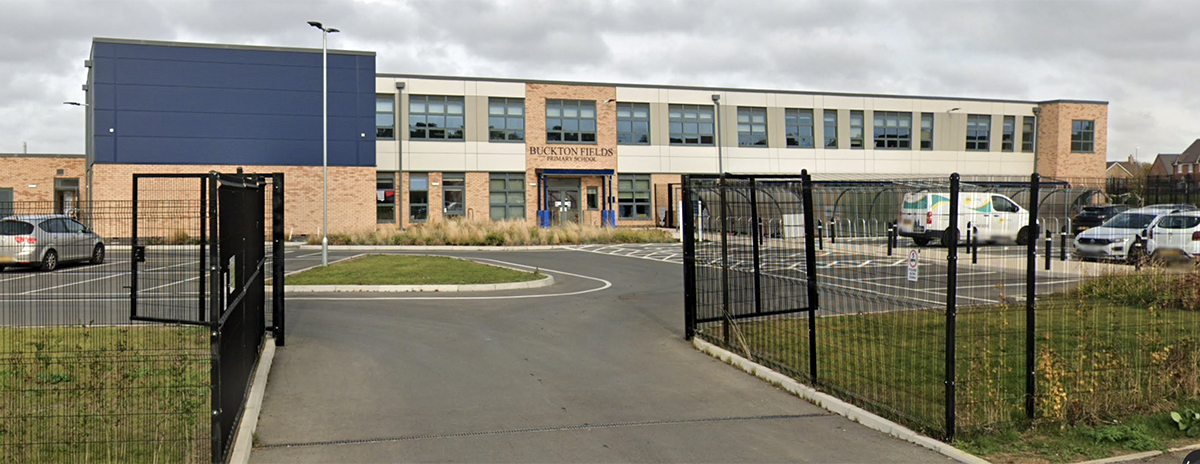
Nevertheless project teams must get to grips with MMC systems and approaches that involve unique health and safety considerations, including key pinch points in design, installation and post-handover operation and maintenance.
Onsite installation can involve heavy loads and hazardous manoeuvres, while factories introduce their own occupational risks. MMC systems and products face challenges around testing and certification, as well as tightening building safety regulations, which have implications for procurement and programming.
“One of the biggest issues, which we find ourselves dealing with regularly, is ensuring that the materials we propose to use in our offsite manufactured solution are fit for purpose and have been properly tested and certified for use,” says Martin Harvey, head of design and technical services at McAvoy.
He gives the example of suppliers that have products tested with masonry and hot-rolled steel but fail to consider testing for compliance in an offsite-manufactured scenario. “Ultimately this results in offsite manufacturers having to carry out a lot of testing of their own,” he adds.
Backing innovation
Recent years have seen the government and private sector clients and contractors align strongly behind MMC, a catch-all term that encompasses anything from volumetric modular to two-dimensional panelisation to kit-of-parts approaches, cross-laminated timber construction and more.
Whitehall continues to drive MMC adoption through various multi-million-pound frameworks and initiatives, such as the presumption in favour of offsite on capital programmes and encouraging its use in official guidance on public sector procurement. But despite increasing momentum, some organisations have raised questions over the safety of offsite approaches. An article published last year by Inside Housing saw the government accused of “suppressing” a report that raised concerns about fire safety and structural integrity of volumetric construction.
The National Fire Chiefs Council issued a position statement at the end of 2022 outlining various concerns with modular buildings, particularly those employing volumetric construction and engineered mass timber products. It warned that buildings are being designed, approved and built “despite a lack of understanding about their performance” and called on the government to tighten rules for testing MMC and to embed competence standards for practitioners working with it.
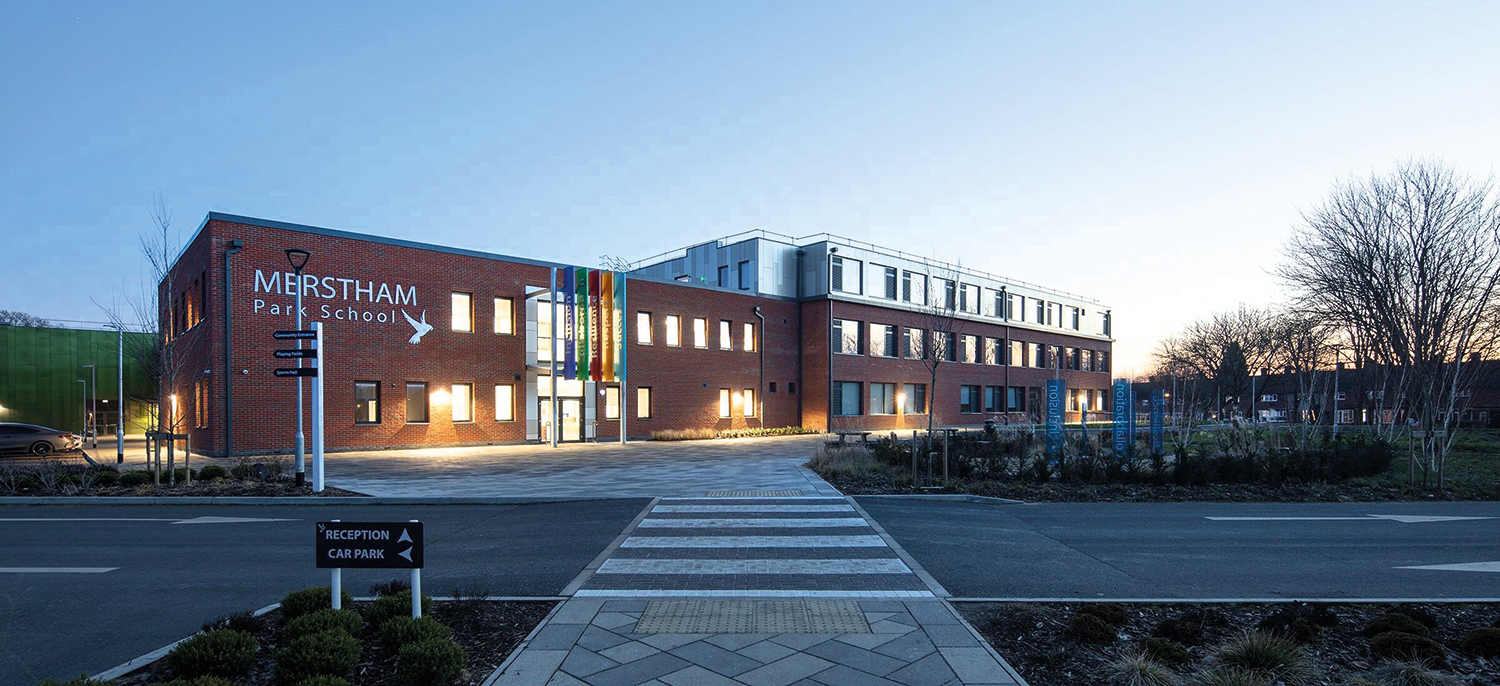
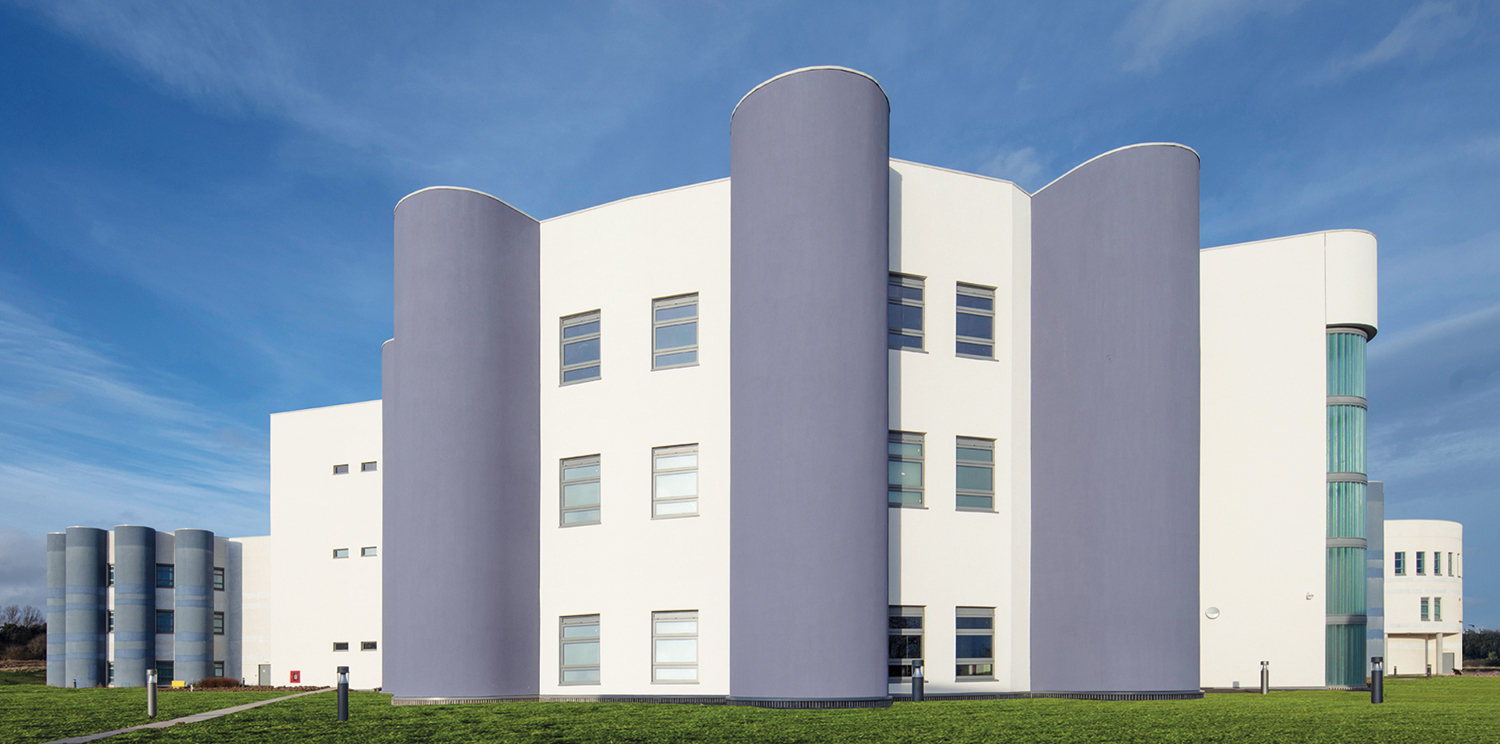
These are worrying developments, but also uncommon and offsite construction is generally associated with better management of health and safety risk. Transferring more work to factories speeds up construction on site, which should reduce accidents associated with the large number of workers and intersecting trades on a traditional project. For example, single storey elements can simply be lifted into place in one piece, while ceilings can be constructed on the ground as part of the roof before being rotated and lifted onto the building.
‘MMC has many benefits’
Stuart Deans, senior associate for health and safety at construction consultant Thomson Gray, says: “MMC has many benefits in terms of reducing time on site. You perhaps don’t have as much hazardous and high-risk work, such as working at height or repetitive tasks associated with musculoskeletal issues.”
Projects working with offsite systems must get to grips with the different processes and products ranging from pre-manufactured 3D and 2D primary structural systems, structural components and non-structural assemblies and sub-assemblies, such as bathroom pods.
Prefabricated elements are often heavy and need to be lifted on and off trucks and around the site using large cranes and other equipment. The use of heavy machinery and need for precise manoeuvres can introduce significant health and safety risk.
According to highly regarded offsite manufacturing specialist McAvoy, MMC demands a thorough assessment of lifting operations, considering factors such as load capacities, environmental conditions and operator competence. It also means factoring in traffic management and vehicular/people segregation.
“The weights and lifting strategies of our sub-assemblies and modules are considered and calculated from the outset through the development of the design in our digital model and our independent structural and lifting consultants,” says Harvey.
Need for properly trained labour
Workers in traditional construction do not necessarily have appropriate skills and competencies to work with MMC. The DfE blamed poor workmanship for structural issues uncovered at the recently condemned schools. This perhaps highlights the need for properly trained labour on site.
As Greg Ward, senior associate for health and safety at construction consultancy Rider Levett Bucknall (RLB), explains, the crossover between manufacturing and construction means sometimes installers have either no, or limited, experience of construction sites.
“There are reasonable simple steps that can be taken to improve this, but it should include an awareness of CDM to ensure individuals understand their responsibilities,” says Ward.
Design and procurement for MMC is typically pulled forward more than traditional construction to ensure detailed design prior to the start of production in the factory.
This gives project managers and safety professionals the opportunity to take a more proactive stance on safety, getting advance buy-in from supply chains and partners and implementing risk assessments well ahead of planned works.
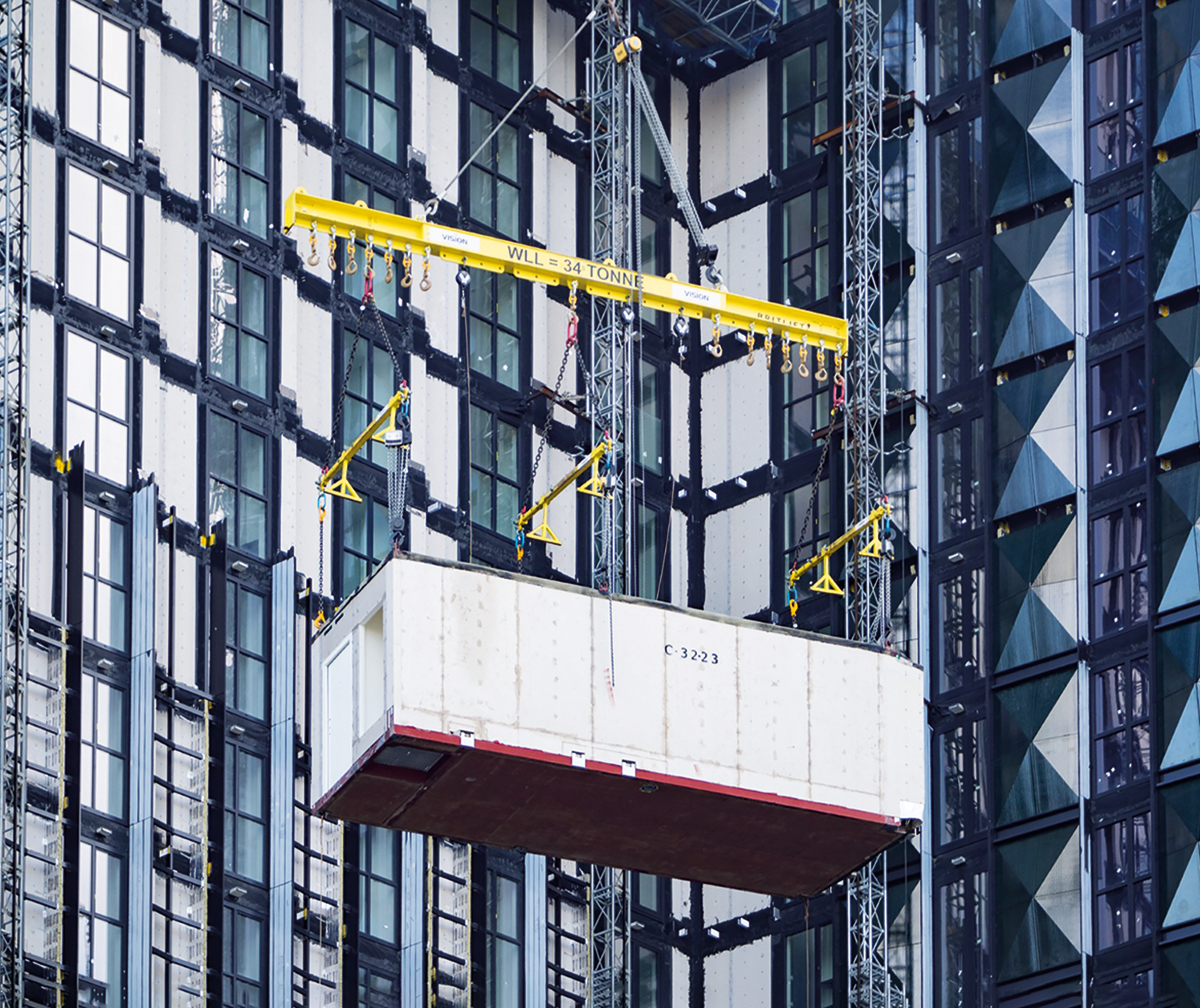
“We like to get the involvement of the manufacturer during RIBA stage two – when you can make big decisions on things like understanding the construction sequence – where cranes would need to go, where loads will be delivered on site and safe areas for laying down, etc,” says Rory Bergin, partner at architect HTA Design, which has helped successfully deliver 12 modular buildings, including Europe’s tallest modular tower in Croydon.
Devising robust safety measures in the early stages, which take in factory build processes, logistics, crane planning, site set-up etc, can ensure that the fast pace of offsite construction, so advantageous for project timelines, doesn’t compromise the safety of workers.
Does MMC work in the real world?
However, the early-doors approach remains a challenge for an industry still unfamiliar with manufacturing principles. Peter Waxman, project director at construction consultancy Gleeds, says: “During RIBA stages the design is always evolving, client needs change, design requirements change, so knowing that a modular unit is going to work with your project is sometimes difficult… Modular construction is a lovely thing to aim for to save time and to win CDM brownie points, but does it actually work in the real world, because construction is a constantly evolving process?”
Moving processes into a factory environment reduces exposure to risks on site, but it also transfers risk from one location to another, making it imperative to gain appropriate understanding and oversight of potential safety issues at manufacturing facilities.
Doing due diligence on suppliers in the factory can ensure they are competent to manufacture systems and have suitable health and safety practices. Additional supervision by the main contractor while they are on site can ensure standards are maintained throughout construction.
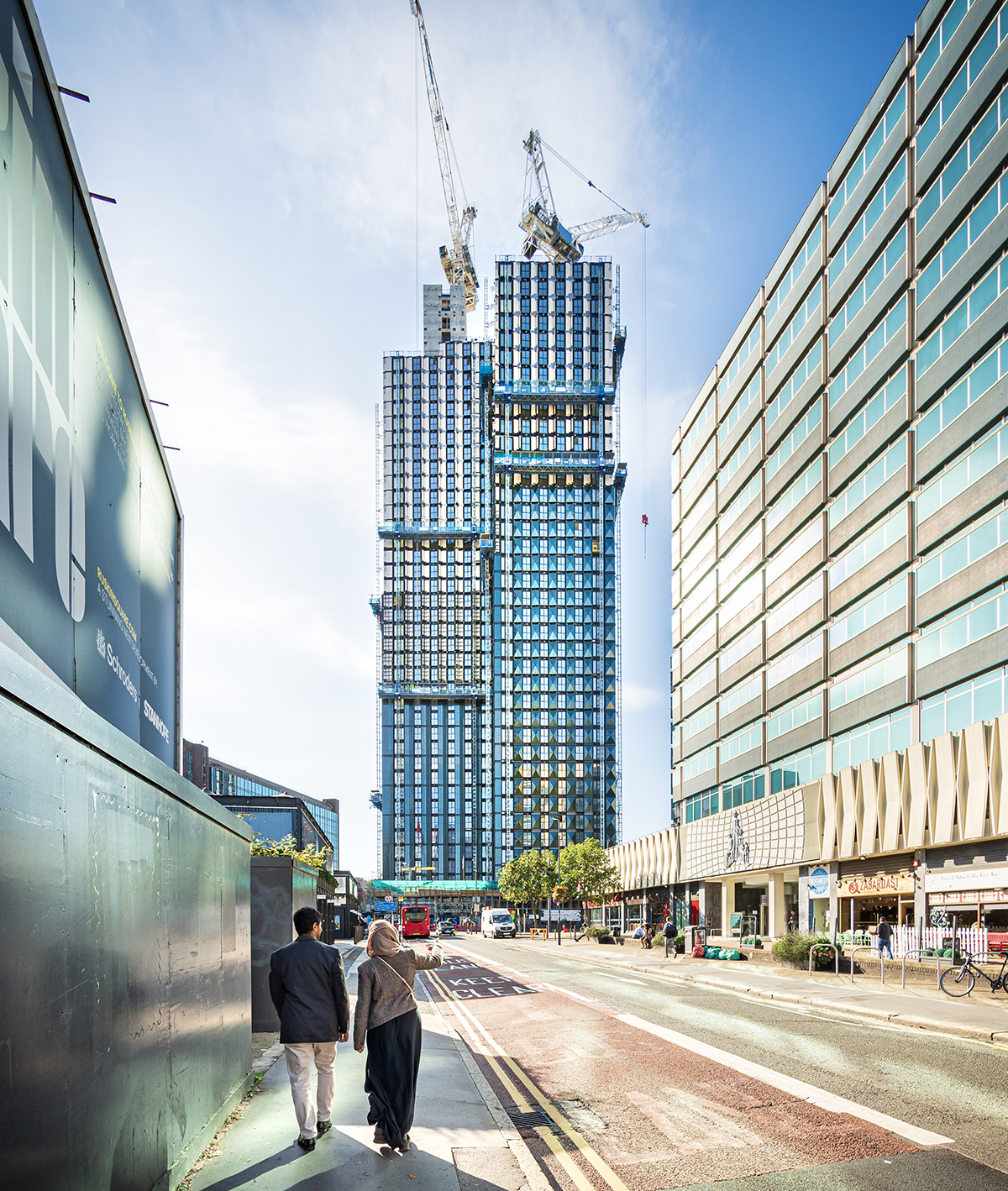
Lifting operations
McAvoy underlines the importance of considering all operations, specifically lifting within the manufacturing facility, as part of the overall planning process. Its facilities are segregated into zones that are planned on a daily, and sometimes hourly, basis.
“Every operative is trained in the work being carried out in that area and all works have standard operating procedures to guide activities,” says Harvey. “Regular toolbox talks and daily meetings help the entire workforce understand the activities planned within the factory.”
Standing at the forefront of construction innovation, MMC buildings challenge traditional structural approaches and behave differently from regular buildings. This places the onus on diligent design and engineering to ensure long-term structural integrity and robustness against fire.
It may be easy to think of volumetric modules as like blocks of Lego that are simply stacked to create different building types, but in reality units must be carefully tailored to handle specific building loads. “A one-size-fits-all approach doesn’t really work because then you end up with things which could be understructured or overstructured,” says Bergin.
Prefabricated structures may require additional consideration around aspects such as impacts from the weather, including snow loadings, or from the surrounding environment. For example, a busy road causing consistent vibration or impacts from vehicles. Temporary works, needed to maintain structural integrity throughout construction, may be more demanding and, according to RLB’s Ward, should be designed and incorporated into the design risk management and construction methodology.
Quality control
Factory production should ensure structural robustness through tighter quality control and tighter tolerances. Production-line repetition also raises the prospect that a defect in a single unit could be replicated across a batch. This has potential implications for long-term building safety. Quality checks are therefore key to picking any issues up in advance.
“Well-run businesses have very good internal QA [quality assurance] and often external QA,” says Bergin. “It’s important that warranty providers visit factories during production
so you don’t have a situation where something is delivered to site and somebody has to open it up to check it is what it is supposed to be.”
MMC structures can create unique situations related to fire safety. Structural safety reporting body CROSS-UK has highlighted the potential for the concealed spread of fire and smoke inside extensive cavities within volumetric modular buildings. Furthermore, the Fire Brigades Union, which represents frontline firefighters, has raised questions about how fires spread in MMC buildings saying that, as a new method of construction, many of the risks are untested.
Collaborative engagement and having the right people at the table during all stages of design and construction – including the fire engineer, principal designer, manufacturer or contractor – can help break down designs and assess them against all aspects of fire.
Design software, such as BIM, is increasingly used in the world of MMC and can identify and visualise any clashes and gaps that could encourage the spread of fire.
“Designers need to consider the fire safety of the completed building, and also the materials. This includes composite materials, and any increased fire risk from the structure being partially complete – and therefore fire protection only partially installed,” says Ward.
Fire testing certificates
MMC products and systems must have the requisite fire testing certificates and documentation. This is a challenge in the UK where there is no unified system for testing the safety of construction products. Instead, assessment is based on conformity with performance requirements set down in various standards, which do not cover all products.
This affects all types of construction product, not just MMC. However, the latter is more onerous due to a lack of historical data and a significant body of knowledge on performance. This has implications for fire safety and insurable risks during construction and post-completion.
Efforts to ramp up scrutiny include the introduction of forthcoming legislation on construction product testing. This is being developed following the publication in spring 2023 of Testing for a Safer Future, an independent review of the construction product testing regime led by Paul Morrell OBE and Anneliese Day KC, by the Department for Levelling Up, Housing and Communities (DLUHC).
Regulatory regime
The new laws will aim to ensure all construction products fall under a regulatory regime and are considered safe. There are additional requirements for a list of ‘safety-critical products’.
In addition, the new building safety regime for higher-risk buildings, established under the Building Safety Act 2022, introduces a new product safety regulator, the Office for Product Safety and Standards. The law places an emphasis on understanding the design strategy to address fire and structural safety and construction products.
Another aspect of the Building Safety Act of particular relevance to MMC is Gateway 2, brought in in October 2023, which requires dutyholders to give greater consideration to procurement and approvals programming.
Dutyholders must now demonstrate to the HSE how they have determined that MMC systems are safe and produce appropriate test evidence and certification before they can obtain gateway clearance ahead of construction and occupation.
“If you’re procuring, there’s going to be a lot of emphasis on contractors to, for example, make sure they’ve engaged with the suppliers of whatever is going to be installed on site and that safety benefits are retained,” says Deans.
Changes to regulation are critical, but guidance and standards also help the industry to develop and improve. The DLUHC, which champions the use of modular construction, recently commissioned a new publicly available standard (PAS) for homes built using MMC. Currently being developed by the British Standards Institution, the PAS will include recommended voluntary technical standards for various MMC categories, as well as quality assurance and compliance processes.
Considered alongside the many specific requirements of MMC builds, project teams now have a growing repertoire of resources needed to help them deliver safe and insurable offsite-constructed buildings.